ERP systems are comprehensive software platforms used to manage and integrate the essential parts of a manufacturing business.
Financials; Supply Chain Management; Material Resource Planning; Production Scheduling… the list goes on.
And, with the right ERP system, they’ll be able to provide you with real-time data, help streamline your manufacturing processes and improve decision-making efficiency.
In this article we’ll examine what an ERP system is, how it can help your manufacturing business and what the best ERP system is for plastics manufacturers.
The Core Functions of ERP in Manufacturing
ERP systems serve as the backbone of a manufacturing operation, ensuring all departments are interconnected.
They handle everything from procurement and inventory management to production scheduling and delivery.
By integrating these functions, ERP systems help manufacturers to minimise errors and reduce time spent on manual processes.
Real-Time Data and Its Impact
Real-time data provided by ERP systems is a game-changer for plastics manufacturers.
It allows businesses to monitor ongoing processes and identify issues as they arise, facilitating immediate corrective actions. This capability is crucial in preventing costly downtime and ensuring that production remains on schedule.
Streamlining Processes Through Integration
ERP systems offer seamless integration across various departments such as sales, finance, and production.
This integration ensures that all teams have access to the same data, improving collaboration and efficiency. For plastics manufacturers, this means smoother operations and better coordination between design, production, and distribution.
Decision-Making Efficiency in ERP
With an ERP system, decision-making becomes more data-driven and less reliant on intuition. The system provides insights into production efficiency, cost management, and market trends. This enables managers to make informed decisions that align with strategic objectives and improve overall business performance.
Why ERP Systems are Essential in Plastics Manufacturing
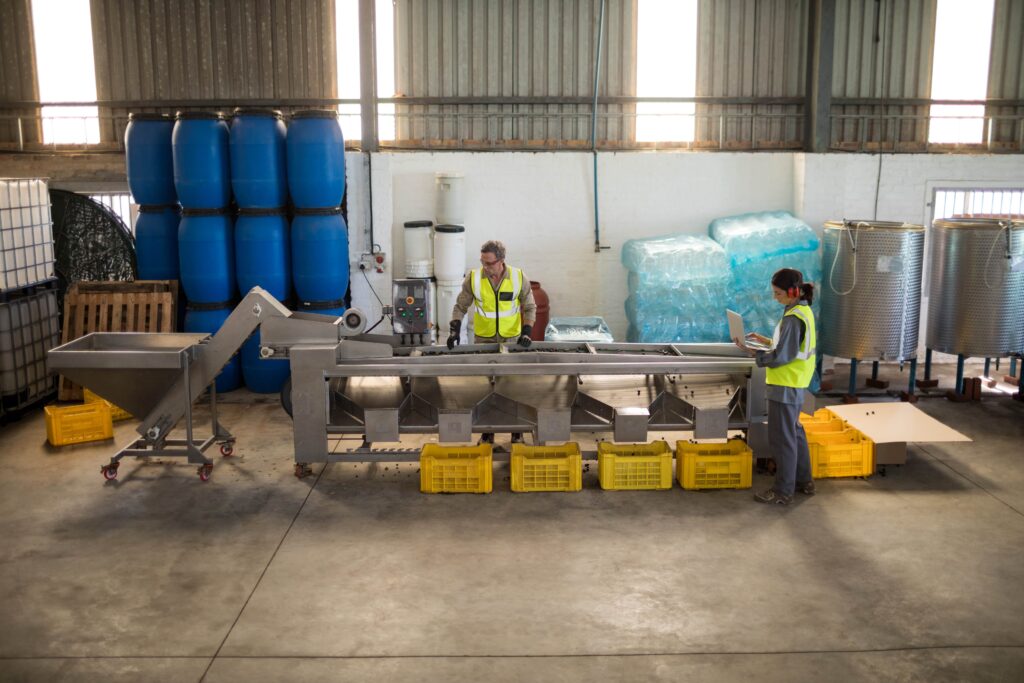
Plastics manufacturing involves intricate processes such as injection moulding and requires precise management of BOMs.
An ERP system tailored for plastics must offer robust capabilities to handle these demands efficiently. Here’s why ERP is indispensable:
- Production Monitoring: Real-time tracking of production processes ensures that manufacturers can maintain optimal efficiency and quickly address any issues that arise. This includes monitoring machine performance and ensuring that production schedules are adhered to, thereby minimising downtime and maximising output.
- Bill of Materials Management: Accurate BOMs are critical for ensuring that the right materials are available at the right time, reducing waste and improving product quality. An ERP system helps in managing complex BOMs by allowing easy updates and modifications, ensuring that production can proceed without interruptions. It is important that the BOM reflects the actual manufacturing process considering things such as runner and sprue weights, cavitation, material blends and regrind usage. A BOM that reflects the process more accurately will assist with maintaining stock accuracy as well as providing a more closely aligned production schedule.
- Quality Control: By integrating quality management within the ERP system, manufacturers can ensure that every product meets stringent standards. This integration allows for continuous monitoring of quality metrics and quick identification of any deviations, thereby maintaining high product standards.
- Cost Efficiency: An ERP system helps to reduce operational costs by optimizing resource usage and improving workflow efficiency. By providing insights into resource allocation and inventory levels, it enables manufacturers to reduce waste and improve profitability.
Key Features of an Effective ERP System for Plastics
When evaluating ERP systems for plastics manufacturing, certain features are essential to ensure that the system meets the industry’s unique needs.
Production Monitoring and Real-Time Data
Production monitoring is a vital feature of any ERP system in the plastics industry. Manufacturers need a system that provides real-time insights into the production floor, allowing them to make informed decisions swiftly. This includes tracking machine performance, production rates, and downtime, which are crucial for maintaining efficiency.
- Machine Performance Tracking: An effective ERP system should provide insights into machine efficiency, helping to identify bottlenecks and areas for improvement. By analysing machine data, manufacturers can optimize maintenance schedules and improve overall equipment effectiveness.
- Production Rates Analysis: Understanding production rates helps manufacturers to plan capacity and manage resources effectively. ERP systems offer tools to analyse production data, enabling better forecasting and planning to meet demand without overproducing.
- Downtime Management: Minimising downtime is critical in plastics manufacturing. ERP systems can help identify the causes of downtime and provide solutions to prevent future occurrences, thereby maintaining a smooth and continuous production process.
Advanced BOM Management
The management of BOMs is particularly complex in the plastics sector due to the variety of materials and components involved. An effective ERP system should allow for detailed BOM management, including the ability to create and modify BOMs quickly and accurately.
- Complex Material Management: Plastics manufacturing often involves a diverse range of materials. ERP systems should support detailed tracking and management of these materials to ensure that the right components are always available for production.
- BOM Customization and Flexibility: The ability to quickly customize and update BOMs is essential. ERP systems should provide tools that allow manufacturers to easily adjust BOMs as products evolve, ensuring continued alignment with production requirements.
- Integration with Supply Chain: Effective BOM management requires integration with the supply chain to ensure timely procurement of materials. ERP systems should facilitate communication with suppliers and manage inventory levels to prevent material shortages.
Integration with Injection Moulding Processes
ERP systems must seamlessly integrate with injection moulding processes to ensure accurate production scheduling and inventory management. This integration helps manufacturers maintain efficient workflows and reduce material waste.
- Production Scheduling Alignment: An ERP system should integrate with injection moulding machines to ensure production schedules are consistently met. This includes managing job orders and coordinating production activities to optimize machine utilization.
- Inventory and Material Management: Integration with injection moulding processes ensures that material usage is tracked accurately. ERP systems can provide insights into material consumption and help reduce waste by optimizing material allocation.
- Workflow Optimization: By aligning injection moulding processes with overall production workflows, ERP systems help to streamline operations. This leads to improved efficiency and reduced lead times, ultimately enhancing customer satisfaction.
Quality and Compliance Management
In industries like plastics, where quality and compliance are non-negotiable, an ERP system should include robust quality management features. This ensures products meet regulatory standards and customer expectations.
- Regulatory Compliance Assurance: ERP systems should include tools that help manufacturers adhere to industry regulations and standards. This includes managing documentation and certifications required for compliance with safety and quality regulations.
- Continuous Quality Monitoring: Effective ERP systems provide real-time quality monitoring, allowing manufacturers to identify and address quality issues promptly. This helps maintain high standards and reduce the risk of product recalls or rework.
- Customer Satisfaction and Feedback: By integrating quality management with customer feedback, ERP systems can help manufacturers understand and meet customer expectations. This leads to improved product quality and customer satisfaction.
DELMIAWorks: A Leading ERP Solution for Plastics
One of the standout ERP solutions for the plastics industry is DELMIAWorks. Known for its comprehensive features and industry-specific capabilities, DELMIAWorks offers numerous advantages for plastics manufacturers.
Key Benefits of DELMIAworks
- Industry-Specific Design: DELMIAWorks is built with the plastics industry in mind, offering features tailored to injection moulding and BOM management. Its design ensures that manufacturers can easily manage the unique challenges faced in plastics production.
- Integrated Quality Management: The system includes tools for quality assurance and compliance, helping manufacturers maintain high standards. This integration ensures consistent product quality and adherence to industry regulations.
- Real-Time Production Monitoring: With DELMIAWorks, manufacturers can track production activities in real-time, enabling quick response to changes and issues. This capability is crucial for maintaining efficiency and meeting production targets.
- Scalability: As businesses grow, DELMIAWorks can scale with them, offering flexible solutions to meet evolving needs. This scalability ensures that the ERP system remains relevant and effective as the business expands.
Advanced Features of DELMIAWorks
- Customisable Dashboards: DELMIAWorks offers customizable dashboards that provide insights into key performance indicators. These dashboards help managers make informed decisions and optimise operations.
- Integrated Financial Management: The system includes comprehensive financial management tools, allowing manufacturers to manage budgets, costs, and profits effectively. This integration ensures that financial data is always aligned with production activities.
- Robust Reporting and Analytics: DELMIAWorks provides advanced reporting and analytics features that offer deep insights into business operations. These tools help manufacturers identify trends, forecast demand, and make strategic decisions.
How to Choose the Best ERP System for Your Business
Selecting the right ERP system involves careful consideration of your specific business needs and objectives. Here are some steps to guide you in making the best choice:
Assess Your Business Needs
Understand your business’s unique requirements and challenges. Consider factors like the size of your operation, the complexity of your production processes, and your growth plans.
- Identify Key Challenges: Begin by identifying the key challenges your business faces. This could include production inefficiencies, quality control issues, or supply chain disruptions. Understanding these challenges will help you select an ERP system that addresses them effectively.
- Evaluate Current Systems: Assess your current systems and processes to identify areas where improvements are needed. This evaluation will provide a baseline for selecting an ERP system that offers the features and capabilities you require.
- Plan for Future Growth: Consider your business’s growth plans and how an ERP system can support them. Choose a system that can scale with your business and adapt to changing needs and market conditions.
Evaluate System Features
Look for ERP systems that offer the features most critical to your operations. These should include production monitoring, BOM management, and integration with your manufacturing processes.
- Prioritise Essential Features: Identify the features that are most important to your operations and prioritize them when evaluating ERP systems. This will help you focus on solutions that align with your business objectives.
- Explore Customisation Options: Consider whether the ERP system can be customized to meet your specific needs. Customisation options can enhance the system’s functionality and ensure it aligns with your unique processes.
- Assess User-Friendliness: Evaluate the system’s user interface and ease of use. A user-friendly system will facilitate adoption and ensure that your team can quickly become proficient with its features.
Consider Vendor Expertise
Choose vendors with a proven track record in the plastics industry. Their experience will be invaluable in helping you implement and optimize the ERP system.
- Research Vendor History: Investigate the vendor’s history and expertise in the plastics industry. Look for case studies and testimonials from other plastics manufacturers to gauge their experience and success.
- Evaluate Support and Training: Consider the level of support and training the vendor provides. A vendor with comprehensive support services will ensure a smooth implementation and help your team maximize the system’s benefits.
- Assess Long-Term Partnership Potential: Choose a vendor that you can see forming a long-term partnership with. This partnership will be crucial as your business grows and your ERP needs evolve.
Plan for Implementation and Training
Successful ERP implementation requires thorough planning and staff training. Ensure that your chosen vendor offers support and resources to facilitate a smooth transition.
- Develop an Implementation Timeline: Work with your vendor to develop a realistic implementation timeline. This timeline should outline key milestones and ensure that the transition is completed without disrupting operations.
- Invest in Staff Training: Allocate resources for staff training to ensure that your team is fully prepared to use the new system. Comprehensive training will help your team become proficient and comfortable with the ERP system.
- Monitor Implementation Progress: Regularly monitor the implementation process to identify any issues or delays. Addressing these promptly will ensure that the transition remains on track and is completed successfully.
Conclusion
Choosing the best ERP system for plastics manufacturing is a significant decision that can impact your business’s efficiency, product quality, and profitability.
ERP Systems like DELMIAWorks, with their industry-specific features and robust capabilities, provide a solid foundation for optimising manufacturing processes.
DELMIAWorks (formerly IQMS) is part of the Dassault Systeme 3DEXPERIENCE platform and is integrated with SOLIDWORKS.
By understanding your business needs, evaluating system features, and planning for successful implementation, you can select an ERP system that enhances your operations and drives growth.
In the competitive world of plastics manufacturing, an effective ERP system is not just an option—it’s a necessity for staying ahead and achieving excellence in production.
Contact us for a initial chat about why DELMIAWorks is the best ERP System for plastics manufacturers.
Want to read more information about DELMIAWorks? Check out this article: