In the world of manufacturing, the term “BOM” is often thrown around, yet it remains a complex concept for many.
BOM stands for Bill of Materials (or Bill of Manufacture), a comprehensive list detailing the raw materials, components, and assemblies required to construct, manufacture, or repair a product.
Understanding the importance of BOMs is crucial for manufacturers aiming to optimize production, improve quality, and leverage enterprise resource planning (ERP) systems for operational efficiency.
Understanding the Bill of Materials
A Bill of Materials (BOM) serves as the blueprint for a product. It outlines every piece, part, and assembly needed, serving as a vital communication tool between departments in a manufacturing facility. The BOM is not just a list but an integral part of the manufacturing process, ensuring that all necessary materials are available and accounted for.
Importance of BOMs in Manufacturing
BOMs are crucial as they provide a clear framework for the entire production process.
They serve as the foundational document that guides the procurement of materials and the scheduling of production activities. Without an accurate BOM, manufacturers would face significant challenges in meeting production deadlines and maintaining product quality.
BOMs also play an essential role in managing costs. By listing every component and its cost, BOMs help manufacturers stay within budget and avoid unnecessary expenditures. This financial oversight is vital for maintaining profitability and competitiveness in the market.
Moreover, BOMs enhance collaboration among different departments. By providing a detailed overview of the materials and processes involved, BOMs ensure that everyone is aligned and working towards the same goal, minimizing errors and improving efficiency.
Components of a BOM
A BOM typically includes several key components, each serving a distinct purpose. The first is a comprehensive list of all materials and parts, along with their specifications and quantities. This list ensures that nothing is overlooked during the production process.
Another crucial component is the assembly instructions. These instructions guide workers on how to put together each part to create the final product, ensuring consistency and quality across production runs.
Finally, a BOM often includes additional information such as supplier details, part numbers, and lead times. This information is vital for managing supply chain logistics and ensuring that materials are available when needed.
Different Levels of BOMs
BOMs can be structured at different levels, ranging from high-level overviews to detailed breakdowns.
High-level BOMs provide a broad overview of the product and its main components, ideal for initial planning and budgeting.
Mid-level BOMs offer more detailed insights into sub-assemblies and their interactions. These BOMs are useful for managing complex products with multiple components and assembly stages.
Detailed BOMs go even further, breaking down each component into its raw materials and individual parts. These BOMs are essential for precision manufacturing, where every detail must be accounted for to ensure quality and compliance.

Types of BOMs
There are several types of BOMs, each serving a different purpose:
Engineering BOM (eBOM)
Created during the product design phase, an eBOM contains the technical specifications and design elements required for a product. It acts as a bridge between the engineering and production teams, ensuring that the product is manufactured according to the intended design.
eBOMs are essential for capturing the design intent and ensuring that all necessary components are included in the final product. They also help in identifying potential design issues early in the process, reducing costly revisions later on.
Additionally, eBOMs facilitate collaboration between designers and manufacturers. By providing a clear and detailed design blueprint, eBOMs ensure that both teams are aligned and working towards the same objectives.
Manufacturing BOM (mBOM)
This version is used during the production process. It includes all the items required to manufacture a product, detailing the processes involved. mBOMs are critical for ensuring that production runs smoothly and efficiently.
mBOMs provide a detailed roadmap for the production team, outlining each step of the assembly process. This level of detail helps in minimising errors and rework, leading to higher productivity and lower costs.
Furthermore, mBOMs play a crucial role in inventory management. By detailing the exact quantities of materials needed, mBOMs help in maintaining optimal inventory levels and reducing waste.
Sales BOM (sBOM)
Used in sales environments, an sBOM includes the finished product and its components that are shipped directly to the customer. sBOMs are essential for managing customer orders and ensuring timely delivery.
sBOMs help in aligning sales and production efforts by providing a clear overview of the products and components involved in each order. This alignment is crucial for meeting customer expectations and maintaining high levels of satisfaction.
Moreover, sBOMs facilitate accurate pricing and cost analysis. By detailing the components and their costs, sBOMs ensure that sales teams can set competitive prices while maintaining profitability.
Configurable BOM (cBOM)
A cBOM is used in environments where products can be customized or configured according to customer specifications. It allows manufacturers to manage variations in products without creating separate BOMs for each configuration.
cBOMs are essential for industries such as automotive and electronics, where customization is a key selling point. By providing a flexible framework, cBOMs enable manufacturers to meet diverse customer needs while maintaining efficiency.
Additionally, cBOMs enhance the sales process by allowing sales teams to generate accurate quotes and proposals quickly. This speed and accuracy are vital for winning new business and retaining existing customers.
The Role of BOM in ERP Systems
A BOM’s integration with an ERP system is essential for managing manufacturing operations effectively. ERP systems like DELMIAWorks facilitate the seamless integration of BOMs, allowing for real-time data tracking and decision-making.
BOM and Inventory Management
When integrated into an ERP system, a BOM helps in various ways, especially in inventory management.
By detailing the components and raw materials needed, a BOM helps manage inventory levels, reducing waste and costs associated with excess inventory.
ERP systems use BOM data to track inventory in real time, ensuring that materials are available when needed and that stock levels are optimized. This real-time visibility is crucial for avoiding production delays and maintaining customer satisfaction.
Additionally, BOMs in ERP systems enable manufacturers to implement just-in-time (JIT) inventory strategies. By aligning inventory levels with production schedules, JIT reduces carrying costs and enhances cash flow.
BOM and Production Planning
BOMs provide a clear picture of what is needed for production, allowing manufacturers to plan and allocate resources effectively. This clarity is essential for optimizing production schedules and ensuring timely delivery.
ERP systems use BOM data to automate production planning processes, reducing the need for manual intervention and minimizing errors. This automation leads to more efficient production runs and higher productivity.
Moreover, BOMs in ERP systems support capacity planning by providing insights into resource availability and constraints. This information is vital for balancing workloads and preventing bottlenecks in the production process.
BOM and Costing and Pricing
A BOM helps determine the cost of materials, which is crucial for setting competitive pricing strategies. By providing detailed cost breakdowns, BOMs enable manufacturers to price their products accurately and competitively.
ERP systems use BOM data to perform cost analysis and identify cost-saving opportunities. This analysis is essential for maintaining profitability and staying competitive in the market.
Furthermore, BOMs in ERP systems support dynamic pricing strategies by allowing manufacturers to adjust prices based on real-time cost fluctuations. This flexibility is crucial for responding to market changes and maximizing revenue.
BOM and Quality Control
With a BOM, manufacturers can ensure that all components meet quality standards before they are used in production. This quality assurance is vital for maintaining product integrity and customer satisfaction.
ERP systems use BOM data to track quality metrics and identify areas for improvement. This tracking helps manufacturers maintain high-quality standards and reduce defects and rework.
Additionally, BOMs in ERP systems support continuous improvement initiatives by providing insights into quality trends and root causes of defects. This information is essential for implementing effective corrective actions and enhancing overall quality.
Creating an Effective BOM
Creating an effective BOM is essential for optimizing manufacturing processes. Here are some best practices:
Detailed and Accurate Information
A BOM should include detailed and accurate information about each component, including part numbers, descriptions, quantities, and unit measurements. This ensures that there is no ambiguity in the materials required for production.
Accurate BOMs prevent production delays and errors caused by incorrect or missing information. By providing precise details, BOMs ensure that production teams have everything they need to complete their tasks efficiently.
Moreover, detailed BOMs facilitate effective communication between departments, ensuring that everyone is on the same page regarding the materials and processes involved in production.
Structured Format
Organise the BOM in a structured format, often hierarchical, where the finished product is at the top level, followed by sub-assemblies and individual components.
This structure helps in understanding the relationship between different parts and how they come together to form the final product.
A well-structured BOM enhances readability and comprehension, making it easier for teams to navigate and understand the document. This clarity is essential for ensuring that production runs smoothly and efficiently.
Additionally, a hierarchical BOM format supports effective change management by providing a clear framework for tracking revisions and updates. This tracking is crucial for maintaining consistency and accuracy, especially when dealing with complex products.
Revision Control
Implement a revision control system for BOMs to track changes and updates. This helps in maintaining consistency and accuracy, especially when dealing with complex products that undergo frequent design changes.
Revision control ensures that all stakeholders have access to the latest version of the BOM, reducing the risk of errors caused by outdated information. This accuracy is vital for maintaining high-quality standards and meeting production deadlines.
Furthermore, a robust revision control system supports effective collaboration by providing a transparent record of changes and updates. This transparency is essential for building trust and ensuring alignment among different teams.
Integration with Other Systems
Ensure that the BOM is integrated with other systems such as ERP, inventory management, and procurement systems. This integration facilitates seamless communication and coordination across departments.
Integrated BOMs enable manufacturers to automate processes and reduce manual intervention, leading to higher efficiency and productivity. This automation is essential for maintaining competitiveness and meeting customer expectations.
Moreover, integrated BOMs support data-driven decision-making by providing real-time insights into production and supply chain activities. These insights are crucial for optimizing operations and achieving business goals.
Regular Review and Update
Regularly review and update the BOM to ensure it reflects the latest product design and production requirements. This practice is essential for maintaining accuracy and relevance in a dynamic manufacturing environment.
Frequent reviews help identify and address discrepancies and errors, reducing the risk of production delays and quality issues. This proactive approach is vital for maintaining high standards and meeting customer expectations.
Additionally, regular updates to the BOM support effective change management by ensuring that all stakeholders are informed of changes and their implications. This communication is essential for maintaining alignment and collaboration among different teams.
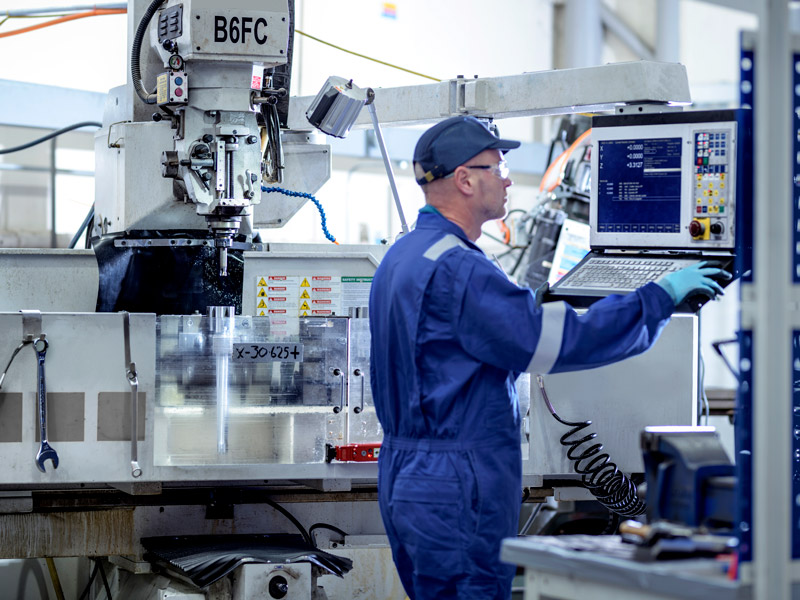
Practical Applications of BOM in Manufacturing
The use of BOMs extends beyond just listing materials. Here are some practical applications:
Streamlining Production Processes
A well-structured BOM helps streamline production processes by providing clear guidelines on the materials and steps needed. This reduces downtime and increases productivity.
BOMs serve as a roadmap for the production team, outlining each step of the assembly process and ensuring that everyone is aligned and working efficiently. This alignment is crucial for meeting production deadlines and maintaining high-quality standards.
Moreover, BOMs support lean manufacturing initiatives by identifying opportunities to eliminate waste and optimize processes. This optimization is essential for reducing costs and increasing profitability.
Enhancing Product Quality
With detailed BOMs, manufacturers can ensure that only quality-approved materials are used, enhancing the overall quality of the final product.
BOMs provide a comprehensive overview of the materials and components involved in production, allowing manufacturers to identify and address quality issues early in the process. This proactive approach is vital for maintaining high standards and meeting customer expectations.
Additionally, BOMs support continuous improvement initiatives by providing insights into quality trends and root causes of defects. This information is essential for implementing effective corrective actions and enhancing overall quality.
Facilitating Communication
BOMs serve as a communication tool between departments, ensuring that everyone is on the same page regarding the materials and processes involved in production.
Clear and accurate BOMs reduce the risk of miscommunication and errors caused by incomplete or incorrect information. This clarity is crucial for maintaining high standards and meeting production deadlines.
Furthermore, BOMs support effective collaboration by providing a transparent framework for sharing information and aligning efforts across different teams. This alignment is essential for achieving business goals and maintaining competitiveness.
Supporting Compliance
For industries with strict regulatory requirements, BOMs help maintain compliance by documenting the materials and components used, ensuring they meet industry standards.
BOMs provide a comprehensive record of the materials and processes involved in production, allowing manufacturers to demonstrate compliance with regulatory requirements. This documentation is essential for avoiding costly penalties and maintaining customer trust.
Moreover, BOMs support effective risk management by identifying and addressing compliance issues early in the process. This proactive approach is vital for maintaining high standards and meeting customer expectations.
Enabling Innovation
BOMs support innovation by providing a clear framework for managing new product development and introduction processes. This framework is essential for bringing new products to market quickly and efficiently.
BOMs provide a comprehensive overview of the materials and processes involved in new product development, allowing manufacturers to identify and address potential challenges early in the process. This proactive approach is vital for maintaining high standards and meeting customer expectations.
Additionally, BOMs support effective collaboration by providing a transparent framework for sharing information and aligning efforts across different teams. This alignment is essential for achieving business goals and maintaining competitiveness.
Conclusion
Understanding and implementing a robust Bill of Materials is crucial for manufacturers aiming to optimize production, improve quality, and leverage ERP systems for better operational efficiency. BOMs are more than just lists; they are the backbone of the manufacturing process, facilitating communication, planning, and decision-making.
By integrating BOMs into ERP systems like DELMIAWorks, manufacturers can achieve greater efficiency, reduce costs, and improve product quality, ultimately driving success in the competitive manufacturing landscape.
Want to learn more about BOMs in DELMIAWorks?
Unsurprisingly, we’ve written a number of articles about BOMs in DELMIAWorks – and you can also access a product tour specifically about BOMs. Follow the links below to learn more.
Product tour: What makes BOMs in DELMIAWorks so unique? which is further supported by an article on the same subject: What makes Bill of Materials so unique.
An overview and introduction to what a BOM is.
A guide to Bill of Materials with a focus on plastics manufacturing.
And an interesting article which examines how an ERP System can be used to manage manufacturing costs (including using BOMs).
There is also an article published back in June 2020 which asks the question, “What is a BOM?“