Regulations for medical device manufacturing are essential for patient safety. However, they can seem overwhelming due to their complexity and frequent updates. These updates often reflect technological advancements and new health concerns.
Manufacturers must balance innovation with compliance, often necessitating a thorough understanding of both domestic and international regulations.
It is crucial to prevent costly delays or rejections due to non-compliance. Such issues can harm the company’s reputation and financial health.
The Importance of Compliance in Medical Device Manufacturing
Compliance with regulatory standards is not just about meeting legal requirements; it’s about building trust with consumers and healthcare providers.
When a medical device meets the necessary standards, it reassures users of its safety and effectiveness.
This trust is paramount in the healthcare industry, where the stakes are incredibly high. Any failure can lead to severe consequences, legally, ethically and morally.
Moreover, compliance also opens doors to global markets.
By following international compliance standards, manufacturers can broaden their reach and access new markets, enhancing their competitive advantage.
This global perspective is increasingly important in a world where healthcare needs are becoming universal, and companies must be agile in their responses to diverse regulatory landscapes.
Therefore, understanding and implementing compliance from the onset not only ensures safety but also supports the long-term strategic growth of the business.
Quality Management and ISO 13485
One of the fundamental aspects of regulatory compliance in medical device manufacturing is adhering to quality management systems (QMS).
ISO 13485 is a globally recognised standard for QMS that ensures consistent design, development, production, and delivery of medical devices. This standard is pivotal as it aligns with many regulatory requirements worldwide, providing a comprehensive framework that manufacturers can rely on to meet their obligations.
Implementing ISO 13485 involves detailed documentation and continuous monitoring of processes. This requires a robust framework that can be effectively managed using ERP software solutions like DELMIAWorks.
These systems help track production metrics, ensure quality control, and facilitate compliance documentation. Furthermore, adhering to ISO 13485 demonstrates a commitment to quality and efficiency, which can enhance a company’s reputation and lead to greater trust among stakeholders, including regulatory bodies, investors, and end-users.
Challenges in Meeting Regulatory Standards
Meeting regulatory standards can be challenging due to the ever-evolving nature of regulations. Manufacturers must stay updated with the latest changes, which can vary across regions. This requires a proactive approach in adjusting processes and adopting new practices as needed.
The dynamics of regulatory environments necessitate a flexible and responsive strategy, where manufacturers must be prepared to pivot quickly in response to new legislation or guidelines.
Moreover, the challenge extends to interpreting these regulations accurately and implementing them effectively across various departments within an organization. This often involves significant resource allocation and can be a substantial burden, particularly for smaller companies.
Staying informed and adapting to changes promptly is essential to avoid the financial and reputational risks associated with non-compliance. Thus, manufacturers must invest in continuous education and a robust infrastructure to support ongoing regulatory adherence.
Using ERP Software for Compliance
ERP software solutions play a pivotal role in medical device manufacturing by providing a centralised platform for managing operations, quality, and compliance. Here’s how they help:
Streamlining Documentation and Reporting
DELMIAWorks ERP system streamlines documentation and reporting processes, which are critical for maintaining compliance.
ERP Systems provide real-time data, enabling manufacturers to generate reports quickly and accurately. This is essential for audits and inspections, where timely access to comprehensive data is crucial.
Moreover, automated documentation reduces the potential for human error, enhancing the accuracy and reliability of compliance reports.
These systems not only improve efficiency but also provide an audit trail that is invaluable during inspections or investigations.
By having all necessary documentation accessible and well-organised, manufacturers can demonstrate compliance with ease, reducing the stress and resource drain typically associated with regulatory audits. This capability is particularly beneficial in an industry where regulations are stringent and the cost of non-compliance can be extraordinarily high.
Enhancing Quality Management
Quality management is at the very core of regulatory compliance.
With ERP software, manufacturers can establish automated quality checks at various stages of production. This ensures that any deviations from standards are promptly identified and addressed, reducing the risk of non-compliance. Automated quality checks also allow for continuous improvement processes, where data from past production cycles can inform future optimizations.
Furthermore, ERP systems, like DELMIAWorks, facilitate a culture of quality by integrating quality management into everyday operations rather than treating it as a separate function.
This integration ensures that quality is a consistent focus, leading to products that not only meet regulatory standards but also exceed customer expectations. By investing in quality management through ERP solutions, manufacturers can enhance their reputation and build long-term customer loyalty.
Facilitating Real-Time Decision-Making
Real-time data provided by ERP systems empowers manufacturing managers and business analysts to make informed decisions swiftly. By having access to up-to-date information, they can adjust production processes to meet quality standards and regulatory requirements effectively.
This agility is crucial in a fast-paced industry where delays can be costly and detrimental to market competitiveness.
Moreover, real-time data supports strategic planning and risk management. By analysing trends and predicting potential issues before they arise, manufacturers can mitigate risks and ensure continuous compliance.
This proactive approach to decision-making not only enhances operational efficiency but also supports sustainable growth in a highly regulated industry.
Overcoming Challenges in Plastics Manufacturing for Medical Devices
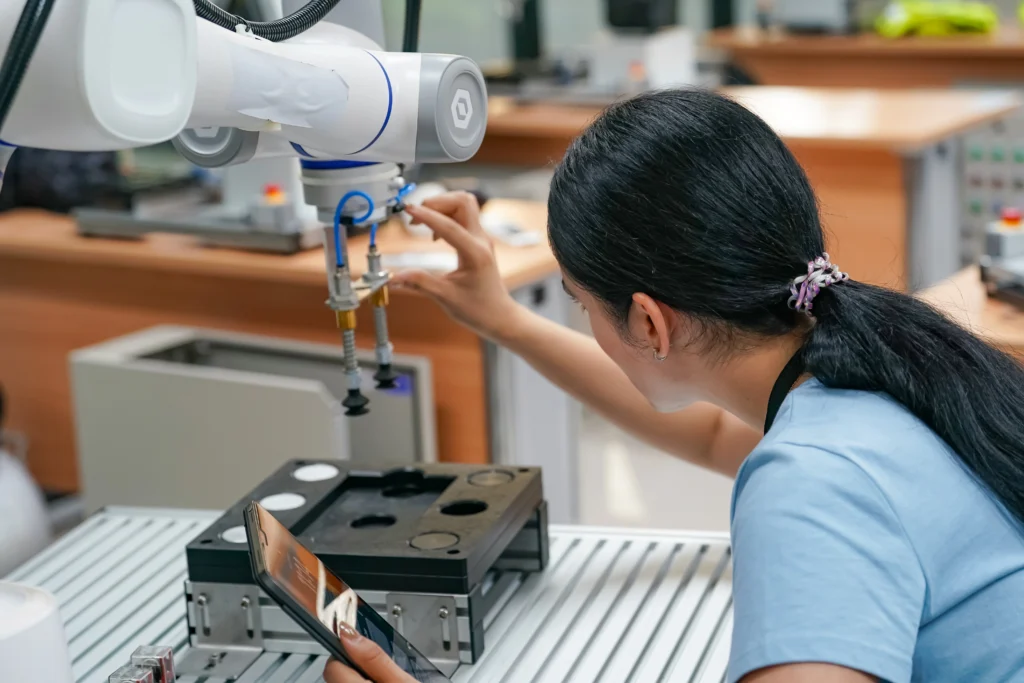
Plastics manufacturing for medical devices presents unique challenges due to strict material requirements and regulatory scrutiny. Ensuring that plastics used are biocompatible and free from contaminants is essential for compliance and safety. The choice of materials can significantly impact the device’s performance and compliance status, making material selection a critical aspect of the manufacturing process.
Additionally, the regulatory focus on environmental sustainability is increasingly influencing material selection. Manufacturers are now required to consider the lifecycle of their products, including the recyclability and environmental impact of the materials used.
This adds another layer of complexity to the already challenging task of material selection, necessitating a balanced approach that considers both regulatory compliance and environmental responsibility.
Material Selection and Compliance
Selecting the right materials is critical. Manufacturers must ensure that the plastics used meet all regulatory requirements for medical devices. This involves thorough testing and validation, often necessitating collaboration with suppliers to guarantee material compliance. Effective supplier management is therefore essential to ensure that materials meet the necessary standards and are delivered consistently.
Furthermore, the validation process must be rigorous and well-documented, as any oversight can lead to non-compliance and potential recalls. This requires a strategic approach to supplier relationships and quality assurance, where open communication and stringent quality checks are prioritised.
By fostering strong partnerships with suppliers, manufacturers can enhance their ability to source compliant materials and maintain a high standard of product quality.
Process Optimisation
Optimising manufacturing processes is key to meeting regulatory requirements efficiently. This includes implementing stringent quality control measures and leveraging ERP systems to monitor production metrics continuously.
By optimising processes, manufacturers can reduce waste, improve efficiency, and ensure consistent product quality, all of which are critical for maintaining compliance.
Furthermore, process optimisation supports innovation by enabling manufacturers to experiment with new technologies and methodologies without compromising compliance.
By maintaining a flexible and adaptable production process, companies can respond more effectively to regulatory changes and market demands. This adaptability is crucial in an industry where technological advancements and regulatory updates are constant.
Practical Strategies for Navigating Regulatory Challenges
Here are some practical strategies for overcoming regulatory challenges in medical device development:
Continuous Education and Training
Keeping abreast of regulatory changes is vital. Regular training for employees on compliance requirements ensures that everyone is informed and prepared to implement necessary changes. This proactive approach minimizes the risk of non-compliance.
Continuous education also fosters a culture of compliance, where employees are encouraged to prioritise safety and quality in all aspects of their work.
In addition, training programs should be dynamic and adaptable, reflecting the latest regulatory updates and industry best practices. By investing in comprehensive training initiatives, manufacturers can empower their workforce to navigate complex regulatory environments confidently and effectively. This not only enhances compliance but also contributes to a more engaged and knowledgeable team.
Collaborating with Regulatory Experts
Working with regulatory experts can provide valuable insights into navigating complex regulatory landscapes. These professionals can offer guidance on best practices and help streamline the compliance process.
Their expertise is especially beneficial for companies looking to enter new markets or develop innovative products that may not fit neatly into existing regulatory frameworks.
Moreover, regulatory experts can assist in interpreting complex regulations and identifying potential compliance risks before they become issues. By leveraging their knowledge and experience, manufacturers can develop more robust compliance strategies and reduce the likelihood of costly regulatory setbacks. This collaboration is an investment in future-proofing the business against the ever-evolving regulatory landscape.
Investing in Advanced ERP Solutions
Investing in advanced ERP solutions, such as DELMIAWorks can significantly enhance compliance efforts.
These systems provide comprehensive tools for managing documentation, quality control, and real-time data analytics, ensuring that manufacturers meet regulatory standards efficiently. By centralising compliance management, ERP solutions reduce complexity and enhance transparency across the organisation.
Furthermore, advanced ERP systems offer scalability and flexibility, allowing manufacturers to adapt their operations to meet changing regulatory requirements seamlessly.
This adaptability is crucial in a dynamic industry where compliance demands can shift rapidly. By investing in ERP technology, companies can position themselves for long-term success by ensuring that compliance is integrated into every aspect of their operations.
The Future of Medical Device Manufacturing
As technology advances, so too will the regulatory landscape.
Manufacturers must remain adaptable and proactive in their approach to compliance. By using ERP systems, investing in continuous education, and collaborating with industry experts, manufacturers can navigate the regulatory challenges of medical device development successfully.
The future of the industry will likely see increased integration of artificial intelligence and machine learning, which will offer new opportunities and challenges in compliance.
In conclusion, understanding and addressing regulatory challenges is essential for medical device manufacturers.
By implementing robust quality management systems, using advanced ERP software, and adopting proactive compliance strategies, manufacturers can ensure that their products meet the highest standards of safety and quality.
These efforts will not only safeguard patient health but also drive innovation and growth in a competitive global market.
By adopting these best practices, manufacturing managers, business analysts, and ERP consultants can enhance operational efficiency and maintain compliance in this highly regulated industry.
As the industry evolves, those who prioritize compliance and innovation will be best positioned to thrive in the future landscape of medical device manufacturing.
Contact us today to learn how DELMIAWorks can help you improve compliance in medical device manufacturing.
Want to learn more about how DELMIAWorks delivers regulatory compliance? Check out these articles for more.