Manufacturing Operations Management (MOM for short) refers to the suite of activities involved in managing the entire production process.
It encompasses everything from the initial planning of resources to the delivery of the final product.
The primary objective of MOM is what could be described as the holy trinity for manufacturers:
- Optimise production efficiency
- Improve product quality
- Reduce operational costs.
By effectively managing these areas, manufacturers can ensure that their production lines are not only efficient but also agile enough to respond to market demands.
Manufacturing Operations Management covers various aspects, such as production scheduling and planning, quality management, and equipment maintenance. Each of these components plays a critical role in the overall success of manufacturing operations.
Key Components of MOM
- Production Management: This involves the planning, coordination, and control of manufacturing processes. The goal is to produce goods efficiently, at the right cost, and with high quality. Effective production management ensures that manufacturing resources are used optimally, reducing waste and increasing throughput. It also involves the continuous assessment and adjustment of production schedules to meet changing demands and minimise downtime.
- Quality Management: Ensures that products meet certain standards and specifications. It’s essential for maintaining customer satisfaction and compliance with regulations. Quality management systems help in identifying defects and implementing corrective actions promptly. This proactive approach not only improves product quality but also enhances brand reputation and customer trust.
- Inventory Management: Involves tracking raw materials, work-in-progress, and finished goods to ensure that production runs smoothly without delays due to shortages. Efficient inventory management reduces holding costs and minimises the risk of stockouts. It also facilitates better demand forecasting and supply chain coordination, which are crucial for just-in-time production strategies.
- Performance Analysis: Involves monitoring and evaluating production processes to identify areas for improvement. This component focuses on collecting and analysing data to drive continuous improvement initiatives. By identifying bottlenecks and inefficiencies, manufacturers can implement targeted strategies to enhance productivity and reduce operational costs.
The Role of Real-Time Data in MOM
The integration of real-time data into manufacturing operations is something we’ve been advocating for a number of years (and is entirely possible with DELMIAWorks ERP and MES System).
It allows managers to make informed decisions quickly and respond to issues as they arise, minimising downtime and enhancing productivity.
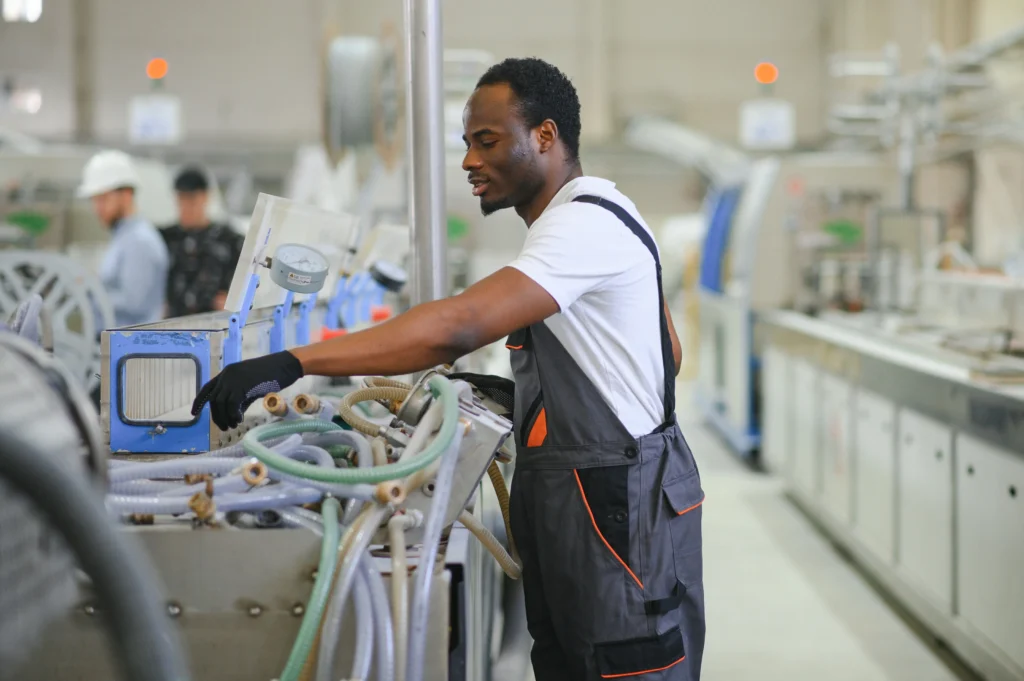
Real-time data provides a dynamic view of the production floor, enabling proactive management of resources and processes. This immediate access to information helps in maintaining optimal production conditions and quickly addressing any deviations from the norm.
Benefits of Real-Time Data
- Improved Decision Making: Access to real-time data helps managers make quick and accurate decisions. By having up-to-date information at their fingertips, managers can better allocate resources, schedule maintenance, and adjust production plans to meet demand fluctuations. This agility is crucial for staying competitive in fast-paced markets.
- Enhanced Productivity: By identifying bottlenecks and inefficiencies, companies can streamline operations and improve output. Real-time data allows for the continuous monitoring of production processes, enabling quick identification of areas that require attention. This proactive approach leads to more efficient operations and higher overall productivity.
- Reduced Downtime: Real-time monitoring can alert managers to potential issues before they cause significant disruptions. Predictive analytics, powered by real-time data, can forecast equipment failures and maintenance needs, reducing unplanned downtime. This not only saves costs but also ensures that production schedules are met without delays.
Differences Between MOM and ERP Systems
While MOM and ERP systems are often discussed interchangeably, they serve different purposes within a manufacturing environment.
Understanding these differences is crucial for optimising your production processes.
MOM focuses on the intricacies of the manufacturing process itself, while ERP systems offer a broader perspective on business operations. Each has its unique strengths, and their combined use can provide a comprehensive solution for managing manufacturing operations.
ERP Systems
Enterprise Resource Planning (ERP) systems are comprehensive software solutions designed to manage and integrate core business processes. They provide a centralised platform for managing finances, supply chain, operations, reporting, manufacturing, and human resources.
ERP systems are instrumental in ensuring that all aspects of the business are aligned and that information flows seamlessly across departments. This integration helps in reducing operational silos and improving overall business efficiency.
Distinguishing MOM from ERP
- Focus: MOM is specifically focused on the manufacturing floor, ensuring production efficiency and quality. In contrast, ERP systems cover a broader range of business functions beyond just manufacturing. This difference in focus means that MOM systems provide more detailed insights into production processes, while ERP systems offer a bird’s-eye view of the entire organisation.
- Functionality: MOM systems provide detailed insights into production processes, such as machine performance and quality control. ERP systems, however, offer a macro perspective, integrating various business processes across departments. This distinction makes MOM systems more suitable for addressing specific manufacturing challenges, while ERP systems are better for overarching business management.
- Integration: While MOM systems can operate independently, they are often integrated with ERP systems to provide a holistic view of both operational and business data. This integration ensures that decisions made on the manufacturing floor are informed by overall business strategies and objectives. It also facilitates better coordination between different departments, leading to more cohesive operations.
Integration of Modern Manufacturing Systems
The integration of advanced manufacturing systems like DELMIAWorks can enhance the functionality of MOM and ERP systems.
DELMIAWorks offers a robust suite of tools that facilitate the seamless operation of manufacturing processes.
By integrating these systems, manufacturers can achieve greater efficiency and flexibility in their operations. This integration enables a unified approach to managing production and business operations, leading to improved outcomes.
Benefits of Integrating DELMIAWorks
- Comprehensive Overview: Offers a unified platform that combines MOM and ERP functionalities, providing a complete view of production and business operations. This comprehensive overview allows for better strategic planning and decision-making, as all relevant information is accessible in one place. The integration streamlines communication between the shop floor and management, leading to more effective coordination.
- Enhanced Efficiency: Streamlines manufacturing processes by offering real-time insights and predictive analytics. This leads to better resource allocation, reduced waste, and optimised production schedules. Manufacturers can quickly adapt to changes in demand and production conditions, maintaining high levels of efficiency and productivity.
- Scalability: Flexible enough to adapt to the changing needs of a growing manufacturing operation. As businesses expand, DELMIAWorks can scale to accommodate increased production volumes and more complex operations. This scalability ensures that manufacturers can continue to meet market demands without compromising on quality or efficiency.
Strategies for Achieving Operational Excellence
Achieving operational excellence requires a strategic approach to manufacturing operations management. Here are some actionable strategies that can help manufacturers optimise their operations and remain competitive. By focusing on continuous improvement and leveraging the latest technologies, manufacturers can achieve significant gains in efficiency and quality.
Streamline Production Processes
- Automate Where Possible: Implement automation technologies to reduce manual intervention and increase production speed. Automation not only speeds up production but also improves accuracy and consistency. By reducing the reliance on manual processes, manufacturers can lower labour costs and minimise the risk of human error.
- Lean Manufacturing Principles: Adopt lean methodologies to eliminate waste and improve process efficiency. Lean principles focus on creating more value with fewer resources, streamlining operations, and enhancing product flow. By eliminating non-value-added activities, manufacturers can increase productivity and reduce costs.
Enhance Product Quality
- Implement Quality Control Systems: Use advanced quality management systems to monitor and improve product standards. These systems help in identifying defects early in the production process, reducing the likelihood of defective products reaching customers. By maintaining high quality standards, manufacturers can enhance customer satisfaction and loyalty.
- Regular Training: Ensure that staff is well-trained in the latest manufacturing techniques and quality standards. Continuous training ensures that employees are equipped with the knowledge and skills needed to maintain high levels of quality and efficiency. Investing in employee development also fosters a culture of continuous improvement and innovation.
Use ERP and MOM Systems
- Integrated Systems: Use ERP and MOM systems in tandem to gain comprehensive insights into both production and business operations. The integration of these systems allows for better coordination and communication across departments, leading to more effective decision-making and strategic planning.
- Regular Updates and Maintenance: Keep software systems updated to take advantage of the latest features and security enhancements. Regular updates ensure that systems remain efficient and secure, protecting against potential disruptions and data breaches. Staying current with the latest technology advancements also enables manufacturers to maintain a competitive edge.
Use Data for Continuous Improvement
- Data Analysis: Regularly analyze production data to identify trends and areas for improvement. By understanding production patterns and performance metrics, manufacturers can implement targeted strategies to enhance efficiency and quality. Data-driven decision-making leads to more informed and effective management of operations.
- Feedback Loops: Establish feedback mechanisms to continuously refine production processes based on real-time data insights. Feedback loops enable manufacturers to respond quickly to changes in production conditions and customer demands. This adaptability is crucial for maintaining competitiveness in dynamic markets.
Conclusion
Understanding and effectively managing manufacturing operations is critical for maintaining competitiveness in today’s industrial landscape.
By leveraging the synergy between MOM and ERP systems, manufacturers can optimise their production processes, enhance product quality, and achieve operational excellence. The integration of advanced systems like DELMIAWorks further augments these efforts, providing a comprehensive platform for managing complex manufacturing operations. Implementing these insights and strategies will equip you to navigate the complexities of manufacturing with confidence and success.
Embracing these tools and methodologies is not just about staying competitive; it’s about setting the standard for operational excellence in the manufacturing industry.
Talk to us to find out more about DELMIAWorks and MOM.