In fast-paced manufacturing landscapes, data is, quite literally, the new gold.
The ability to collect, analyse, and act on real-time data from process equipment can significantly benefit manufacturers. This capability helps them optimise efficiency, reduce costs, and enhance product quality.
This is especially pertinent at a time when UK manufacturers are facing increased National Insurance contributions next month.
By using smarter automation, manufacturers can shift from reactive to proactive decision-making.
This helps ensure that every machine, process, and resource operates at peak performance.
Harnessing the power of process equipment data
Most modern manufacturing equipment has sensors and IoT capabilities that produce large amounts of data.
When used correctly, this data provides actionable insights into:
- Machine Performance: Predict maintenance needs before breakdowns occur.
- Production Efficiency: Identify bottlenecks and optimise workflows.
- Quality Control: Detect anomalies early and prevent defects.
- Energy Consumption: Reduce waste and improve sustainability.
However, data alone is not enough.
Without a centralised system to collect and analyse information, manufacturers miss valuable chances to optimise their shop floor processes.
This is where DELMIAWorks Manufacturing ERP comes in.
And, on Thursday 3rd April there is an opportunity to join Dassault Systemes, the developer of DELMIAWorks, to learn how connecting DELMIAWorks with your process equipment data can streamline operations, boost efficiency and support smarter decision-making.
Register for ‘Smarter Automation – Bridging Your Process Equipment and Enterprise Management Solution’
If you can’t attend live, a recording will be sent to registrants through email after the webinar.
More about DELMIAWorks: the key to smarter manufacturing
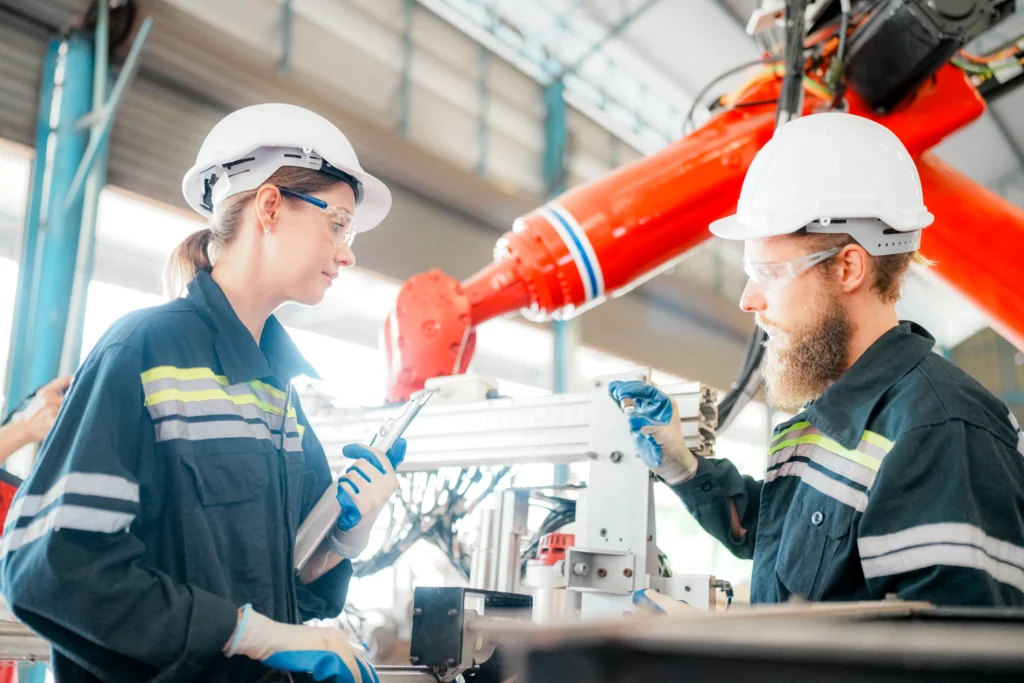
DELMIAWorks, is a comprehensive Manufacturing ERP (Enterprise Resource Planning) system, which provides the visibility and control manufacturers need to make data-driven decisions.
Here’s how DELMIAWorks can enhance smarter automation:
Real-Time Data & MES System
DELMIAWorks can seamlessly connect to process equipment, collecting real-time production data to provide up-to-the-minute insights. This eliminates manual data entry and ensures accuracy in tracking key performance indicators (KPIs).
Predictive Maintenance
By analysing machine data, manufacturers can implement predictive maintenance, reducing downtime and increasing overall equipment effectiveness (OEE). No more unexpected breakdowns – just smooth, uninterrupted production.
Enhanced Quality Management
DELMIAWorks integrates quality control directly into the manufacturing process, automatically flagging deviations and ensuring products meet stringent standards. This leads to fewer defects, lower scrap rates, and higher customer satisfaction.
Optimised Production Scheduling
By using real-time data, DELMIAWorks enables optimised production scheduling and planning. This ensures that resources, labour, and materials are utilized efficiently, improving on-time delivery rates and reducing waste.
End-to-End Visibility
DELMIAWorks offers a complete view of manufacturing operations, from the shop floor to the final destination. This enables manufacturers to spot inefficiencies, optimise workflows, and promote continuous improvement.
Smarter Automation: Your Competitive Edge
Manufacturers who embrace data-driven automation with solutions like DELMIAWorks gain a significant competitive edge. They achieve:
- Higher productivity through streamlined processes.
- Lower operational costs by reducing downtime and waste.
- Improved decision-making with real-time insights.
- Greater flexibility to respond to market demands.
In today’s world, manufacturing excellence relies on efficiency, agility, and quality. Using process equipment data and smart ERP software solutions is essential, not optional.
Ready to take your manufacturing operations to the next level? Start optimising with DELMIAWorks by contacting us.
Want more about smart automation & DELMIAWorks? Read these articles: