Standardisation in manufacturing refers to the practice of establishing uniform procedures and guidelines to ensure consistency across different production sites.
This approach is essential for several reasons.
Why standardisation is important
Enhancing quality control
Standardisation is a key factor in maintaining consistent quality across all production lines.
By implementing standardised procedures, manufacturers can reduce variability in processes, ensuring that every product meets the same quality standards.
This consistency is vital for building customer trust, maintaining a strong brand reputation and quality standard compliance.
Moreover, standardised quality control procedures facilitate the early detection of defects, allowing for timely interventions and minimising the risk of defective products reaching the customer.
Furthermore, standardised processes provide a framework for continuous quality improvement. By analysing data from standardised operations, manufacturers can identify areas where quality can be enhanced and implement targeted improvements.
This proactive approach to quality control not only maintains high standards but also drives innovation and competitive advantage.
As mentioned earlier in this section, standardisation also supports regulatory compliance by ensuring that quality control measures meet industry standards and legal requirements. This reduces the risk of non-compliance and associated penalties, safeguarding the company’s reputation and financial standing.
Streamlining operations
Standardisation simplifies operations by creating clear and uniform procedures for employees to follow. This not only speeds up the production process but also minimises errors and rework.
With standardised processes, workers are better equipped to identify and resolve issues, leading to more efficient manufacturing operations. In addition, standardised operations reduce training time for new employees, as clear guidelines and processes are already in place, facilitating quicker onboarding and productivity.
By reducing process complexity, standardisation also enhances operational predictability. This predictability allows for more accurate production planning and resource allocation, optimizing the use of materials and labour.
As a result, manufacturers can achieve higher throughput and lower production costs, contributing to improved profitability.
Standardised operations also enable better coordination and communication across different departments and sites. With everyone following the same procedures, there is less room for miscommunication and misunderstanding, leading to smoother workflows and fewer disruptions in production.
Facilitating lean manufacturing
Lean manufacturing emphasises the elimination of waste and the maximisation of productivity.
Standardisation plays a critical role in lean initiatives by providing a foundation for continuous improvement. With standardised processes, manufacturers can easily identify inefficiencies and implement changes to enhance productivity and reduce waste.
Standardisation also supports the implementation of lean tools, such as Kaizen and 5S, by providing a consistent framework for their application.
Moreover, standardised processes enable the accurate measurement of key performance indicators (KPIs), facilitating data-driven decision-making. This data-driven approach allows manufacturers to prioritise improvement efforts based on their impact on productivity and waste reduction, ensuring that resources are allocated effectively.
In addition, standardisation supports the development of a culture of continuous improvement. By involving employees in the standardisation process and encouraging their input on potential improvements, manufacturers can foster a sense of ownership and engagement. This collaborative approach drives innovation and motivates employees to contribute to the ongoing success of lean initiatives.
Ensuring Compliance
In the highly regulated manufacturing industry, compliance with industry standards and regulations is crucial.
Standardisation helps ensure that all processes adhere to these requirements, reducing the risk of non-compliance and potential penalties. By establishing standardised procedures that align with regulatory requirements, manufacturers can streamline compliance efforts and reduce the administrative burden associated with maintaining compliance.
Standardisation also facilitates audits and inspections by providing clear documentation of processes and controls. This documentation not only demonstrates compliance to regulatory bodies but also provides a valuable resource for internal audits and continuous improvement efforts.
Furthermore, standardised compliance processes enhance the organisation’s ability to respond to changes in regulations.
By having a consistent framework in place, manufacturers can quickly adapt to new requirements and implement necessary changes across all sites, minimising disruption and ensuring ongoing compliance.
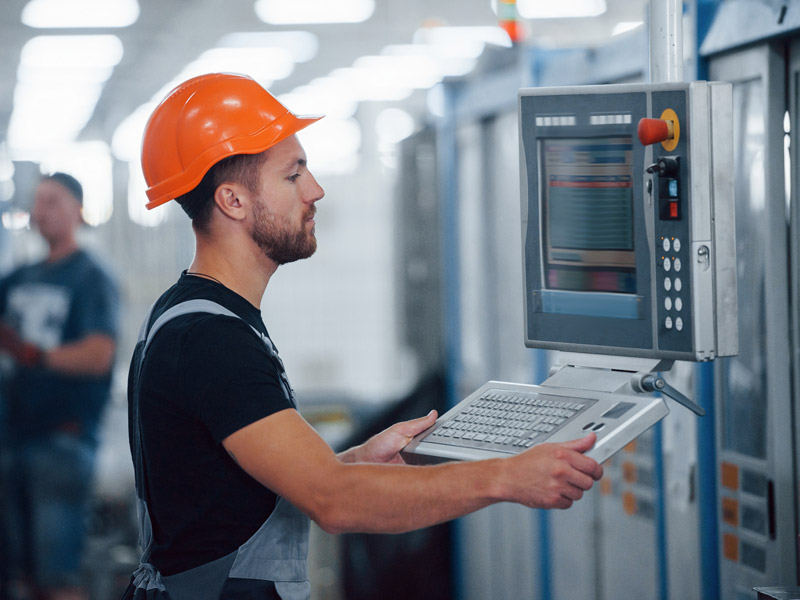
The role of ERP systems in standardisation
These systems provide a centralized platform for managing and optimising production activities, making it easier to implement and maintain standardised procedures.
Centralised data management
ERP systems offer a centralised database that stores all relevant data related to production processes, inventory, and quality control.
This is particularly true with DELMIAWorks manufacturing ERP, which features a single database.
This centralised data management ensures that all sites have access to the same information, promoting consistency and accuracy across the organization.
By having a single source of truth, manufacturers can reduce data discrepancies and ensure that decisions are based on accurate and up-to-date information.
Centralised data management also supports effective resource planning and allocation.
With visibility into inventory levels and production schedules, manufacturers can optimise the use of materials and minimise stockouts or overproduction.
This optimisation contributes to cost savings and improved operational efficiency.
Furthermore, centralised data management enhances traceability and accountability.
By tracking production activities and quality control measures in a single system, manufacturers can quickly identify the source of any issues and take corrective action. This traceability is particularly important in regulated industries, where detailed documentation is required to demonstrate compliance.
Real-time data and decision-making
One of the significant advantages of ERP systems is their ability to provide real-time data.
This feature allows manufacturers to monitor production activities continuously and make informed decisions quickly. Real-time data also enables the identification of potential issues before they escalate, ensuring that standardised processes remain effective. By having access to real-time insights, manufacturers can respond proactively to changes in demand or production conditions, minimising disruptions and maximising efficiency.
Real-time data also supports predictive maintenance efforts.
By monitoring equipment performance and identifying patterns of wear and tear, manufacturers can schedule maintenance activities before breakdowns occur. This proactive approach reduces downtime and extends the lifespan of equipment, contributing to cost savings and improved productivity.
In addition, real-time data facilitates collaboration across different departments and sites. By providing visibility into production activities and performance metrics, ERP systems enable teams to work together effectively and make coordinated decisions. This collaboration enhances problem-solving and drives continuous improvement efforts.
Integration with lean manufacturing
ERP systems can be integrated with lean manufacturing principles to enhance process efficiency. By providing insights into production workflows, ERP systems help manufacturers identify areas for improvement and implement lean strategies effectively.
This integration supports the continuous improvement of standardized processes, further optimising production operations. By aligning ERP capabilities with lean initiatives, manufacturers can drive waste reduction and productivity gains across the organization.
Integration with lean manufacturing also enables better alignment between production and business objectives. By linking production activities with key performance indicators, manufacturers can ensure that lean efforts are focused on areas that deliver the greatest impact on business performance. This alignment supports strategic decision-making and enhances the organisation’s ability to achieve its goals.
Furthermore, ERP systems provide the tools needed to measure and track the success of lean initiatives. By analysing data from standardised processes, manufacturers can assess the effectiveness of lean strategies and make data-driven decisions to refine and enhance their approach.
This iterative process supports the ongoing success of lean initiatives and drives continuous improvement.
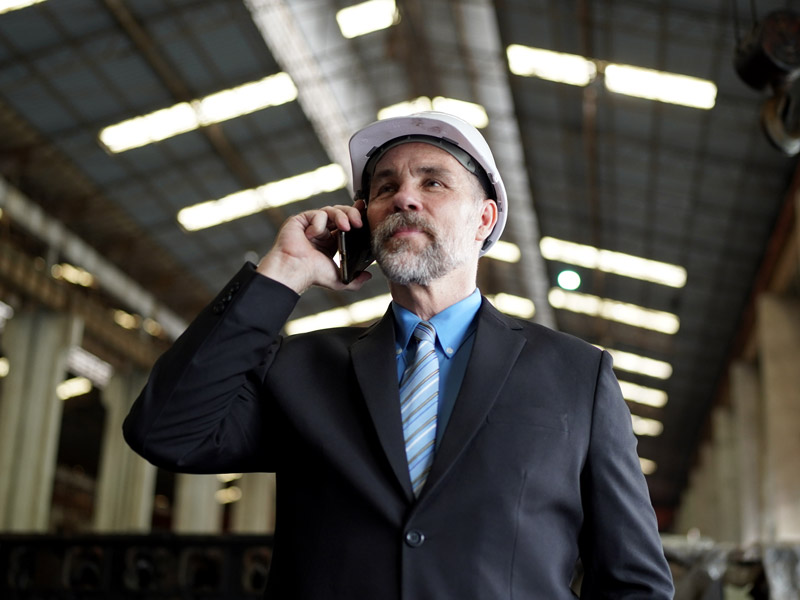
Implementing standardisation across multiple sites
Successfully implementing standardisation across multiple manufacturing sites requires careful planning and execution. Here are some actionable strategies to achieve this goal:
Conduct a process audit
Start by conducting a thorough audit of existing processes at each manufacturing site. Identify variations and inefficiencies that need to be addressed. This audit will serve as a baseline for developing standardised procedures. Involve cross-functional teams in the audit process to gain a comprehensive understanding of current practices and potential areas for improvement.
The process audit should also assess the alignment of current processes with business objectives and regulatory requirements. By evaluating these factors, manufacturers can ensure that standardized procedures support strategic goals and compliance efforts. This alignment is crucial for maximising the impact of standardisation on business performance.
Additionally, the audit process should include a review of existing documentation and training materials. By identifying gaps and inconsistencies in these resources, manufacturers can develop comprehensive and accurate documentation to support standardized processes.
Develop Standard Operating Procedures (SOPs)
Create detailed Standard Operating Procedures (SOPs) for each process. These SOPs should outline step-by-step instructions, quality control measures, and safety guidelines. Ensure that all employees are trained on these procedures to maintain consistency. Involve employees in the development of SOPs to leverage their expertise and ensure that procedures are practical and effective.
SOPs should also include clear roles and responsibilities for each step of the process. By defining these roles, manufacturers can ensure accountability and streamline communication and coordination efforts. This clarity supports efficient operations and reduces the risk of errors or misunderstandings.
Furthermore, SOPs should be regularly reviewed and updated to reflect changes in processes, technology, or regulations.
By maintaining up-to-date SOPs, manufacturers can ensure that standardised procedures remain relevant and effective in achieving business objectives.
Leverage technology
Utilise ERP systems to facilitate the implementation of standardized processes. These systems provide the tools needed to monitor, analyse, and optimise production activities. Ensure that all sites are equipped with the necessary technology and that employees are trained to use it effectively. By providing ongoing training and support, manufacturers can maximize the benefits of ERP systems and drive the success of standardisation efforts.
Technology can also support the automation of routine tasks, reducing the burden on employees and minimising the risk of errors. By automating processes such as data entry or inventory management, manufacturers can improve accuracy and free up resources for more strategic activities.
In addition, technology can facilitate remote monitoring and management of production activities. By providing real-time insights into operations across different sites, manufacturers can ensure that standardised processes are consistently implemented and that any issues are quickly addressed.
Foster a culture of continuous improvement
Encourage a culture of continuous improvement by involving employees in the standardisation process. Solicit feedback and suggestions from workers to identify areas for improvement and implement changes. This collaborative approach fosters a sense of ownership and commitment to maintaining standardised processes. By recognising and rewarding contributions to improvement efforts, manufacturers can motivate employees and drive engagement.
A culture of continuous improvement also supports innovation by encouraging employees to challenge the status quo and explore new ways of working. By empowering employees to experiment with new ideas and approaches, manufacturers can drive ongoing improvements in efficiency and quality.
Furthermore, a continuous improvement culture enhances organizational agility by enabling manufacturers to respond quickly to changes in the market or production conditions. This agility supports long-term success in a competitive industry and positions the organization for future growth and development.
Monitor and evaluate performance
Regularly monitor and evaluate the performance of standardised processes to ensure their effectiveness. Use real-time data provided by ERP systems to track key performance indicators (KPIs) and make data-driven decisions to optimise operations continually. By setting clear performance targets and regularly reviewing progress, manufacturers can ensure that standardisation efforts deliver the desired outcomes.
Performance evaluation should also include a review of employee feedback and suggestions for improvement. By incorporating this input into decision-making, manufacturers can ensure that standardised processes remain relevant and effective in meeting business objectives.
Additionally, performance monitoring supports the identification of best practices and the sharing of these practices across different sites. By leveraging the insights gained from performance evaluation, manufacturers can drive continuous improvement and enhance the overall success of standardisation efforts.
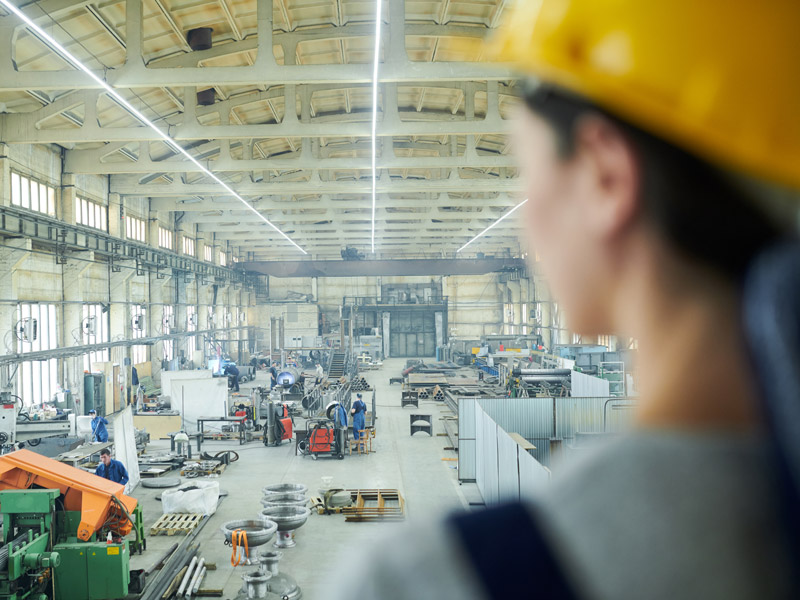
Conclusion
Standardising processes across multiple manufacturing sites is essential for achieving operational efficiency, maintaining consistent quality, and ensuring compliance. By leveraging ERP systems and lean manufacturing principles, manufacturers can streamline their operations and enhance productivity. Implementing standardisation requires careful planning, but the benefits it brings to production efficiency and product quality are well worth the effort.
Incorporating these strategies into your manufacturing operations will not only improve your bottom line but also position your organization for long-term success in a competitive industry. By focusing on standardisation, you can unlock new levels of efficiency and quality, setting your manufacturing sites apart from the competition. Embrace the power of standardisation to drive innovation, enhance customer satisfaction, and secure a sustainable future for your organisation.
Check out this article to learn more about multi-site manufacturing operations.
Learn more about DELMIAWorks manufacturing ERP
Contact us to see how DELMIAWorks manufacturing ERP can help you standardise manufacturing processes.