Material Requirements Planning, commonly known as MRP, is a system used to manage manufacturing processes and get a better view of business resources required to facilitate these processes.
It uses software to help manufacturers discover what materials, labour, machine capacity, packaging, and other elements they need.
It also shows how much is needed and when based on business objectives. This helps meet production requirements, but also prevents overstocking and improves cashflow.
MRP systems function as the backbone of manufacturing operations, coordinating all elements of production to ensure seamless execution. The system ensures that materials are available for production and products are available for delivery to customers, reducing waste and optimizing resources.
The Core Purpose of MRP Systems
At its core, MRP aims to streamline manufacturing operations by ensuring that there is enough inventory to meet production demands while minimising waste and reducing carrying costs.
This is achieved by calculating the materials and components required to manufacture a product and scheduling their procurement and production.
MRP systems help manufacturers avoid the high costs of making too much or too little. This allows them to respond better to market needs.
Efficient inventory management using MRP can greatly reduce lead times. This helps manufacturers meet customer deadlines and adjust to changes in demand.
MRP Systems and Their Importance
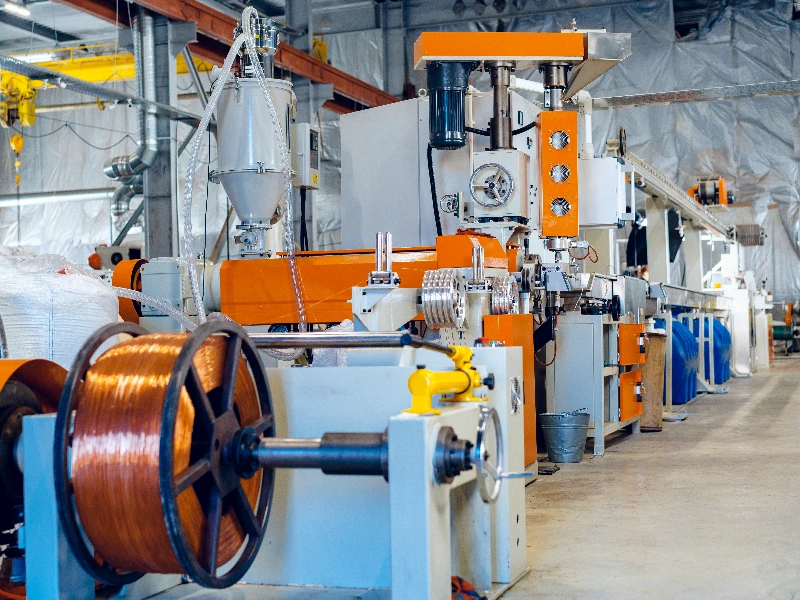
MRP systems are an integral part of manufacturing operations. They help manufacturers manage their inventories, production schedules, and procurement processes more effectively.
By using MRP systems, manufacturers can get the right materials when they need them. This helps reduce downtime and improve efficiency.
This level of precision in planning is not only crucial for maintaining productivity but also for optimizing financial performance by lowering costs associated with excess inventory and production delays. Furthermore, MRP systems foster better collaboration and communication across departments, aligning production goals with business objectives and customer expectations.
Importance of Material Requirement Planning
Material requirement planning is crucial in manufacturing for several reasons:
Improving Production Efficiency
By accurately forecasting material needs, MRP systems help manufacturers avoid production delays caused by material shortages. This ensures a smooth production flow and improves overall efficiency. The predictive capabilities of MRP allow for proactive adjustments, preventing bottlenecks before they occur.
This proactive approach boosts productivity. It also helps manufacturers use resources better. This ensures that both people and machines are used to their full potential.
Reducing Inventory Costs
MRP systems help in optimising inventory levels, which means manufacturers can hold just enough inventory to meet production needs without overstocking.
This reduces inventory carrying costs and minimizes waste. By keeping a small amount of stock, companies can free up money tied up in extra inventory. This helps improve cash flow and financial health.
Additionally, minimising waste aligns with sustainable practices, as it reduces the environmental impact associated with excess production and disposal of unused materials.
Organisations with smaller warehouses or limited space can also benefit greatly from operating in a more JIT (Just-In-Time) manner that can be supported by effective utilisation of MRP.
Enhancing Customer Satisfaction
With MRP, manufacturers can ensure timely delivery of products to customers by aligning production schedules with customer demand. This leads to improved customer satisfaction and stronger business relationships.
Meeting delivery promises consistently builds trust and enhances a manufacturer’s reputation in the market, which can lead to repeat business and positive word-of-mouth referrals.
Moreover, the flexibility to adapt production schedules to meet urgent customer needs can set a manufacturer apart in a competitive landscape.
Supporting Decision-Making
MRP systems provide real-time data and insights, allowing manufacturers to make informed decisions. This data-driven approach helps in identifying potential issues, optimising production processes, and improving overall operational efficiency.
Access to accurate and timely information enables managers to conduct scenario analyses, preparing for various market conditions and uncertainties. By using these insights, manufacturers can strategize effectively, ensuring long-term sustainability and growth.
Key Features of MRP Systems
MRP systems come with a variety of features designed to support manufacturing operations. Some of these key features include:
Inventory Management
MRP systems track inventory levels and help manufacturers maintain optimal stock levels. This prevents overstocking and stockouts, ensuring that materials are always available when needed. Effective inventory management also allows for better supplier relationships, as manufacturers can order materials more predictably and in alignment with production cycles.
Additionally, by tracking inventory movements, MRP systems can provide valuable data for evaluating supplier performance and negotiating better terms.
Production Scheduling
MRP systems assist in creating detailed production schedules that align with demand forecasts. This ensures that production runs smoothly and efficiently, with minimal downtime. By optimising production timelines, MRP systems help manufacturers maximize equipment utilisation, reducing idle time and increasing throughput. Furthermore, the ability to adjust schedules quickly in response to unforeseen changes enhances a manufacturer’s agility and responsiveness to market demands.
Demand Forecasting
By analysing historical data and market trends, MRP systems help manufacturers forecast future demand accurately. This enables better planning and resource allocation. Accurate demand forecasting minimises the risk of stockouts or overproduction, ensuring that manufacturing operations align closely with actual market needs. This foresight allows manufacturers to plan strategic investments in capacity, technology, or personnel, ensuring they are well-prepared for future growth.
Capacity Planning
MRP systems assess production capacity and help manufacturers determine if they can meet demand with their current resources. This helps in identifying bottlenecks and planning for capacity expansion if necessary. By understanding capacity constraints, manufacturers can make informed decisions about hiring, equipment purchases, or outsourcing to meet production goals. This strategic planning is essential for scaling operations sustainably and maintaining competitive advantage.
The Role of DELMIAWorks in MRP
DELMIAWorks is a comprehensive ERP solution that includes robust MRP System capabilities.
It is designed to address the unique needs of manufacturers by providing tools for inventory management, production scheduling, and quality control.
DELMIAWorks integrates seamlessly with various manufacturing processes, offering a holistic approach to managing operations.
By combining MRP with other ERP functionalities, it provides a comprehensive view of the entire manufacturing ecosystem, enabling better coordination and strategic decision-making.
How DELMIAWorks Enhances MRP
DELMIAWorks integrates seamlessly with MRP systems, offering a unified platform for managing all aspects of manufacturing operations.
Its features include real-time data analysis, automated scheduling, and advanced reporting capabilities, which help manufacturers optimise their production processes and improve operational efficiency.
By providing insights into every facet of the manufacturing process, DELMIAWorks empowers manufacturers to identify inefficiencies and implement improvements swiftly. The advanced reporting tools also facilitate compliance with industry standards and regulations, ensuring that manufacturers maintain high quality and safety standards.
Practical Strategies for Implementing MRP
Implementing an MRP system can be challenging, but with the right strategies, manufacturers can maximise its benefits. Here are some practical tips for successful MRP implementation:
Conduct a Thorough Needs Assessment
Before implementing an MRP system, manufacturers should conduct a comprehensive assessment of their needs and goals. This will help in selecting the right system that aligns with their specific requirements. Understanding the unique challenges and opportunities within a manufacturing operation ensures that the chosen MRP system addresses critical pain points. Involving key stakeholders in this assessment process can also foster buy-in and ensure that the system meets the needs of all users.
Train Your Team
Proper training is essential for successful MRP System implementation.
Manufacturers should ensure that their team is well-versed in using the MRP system and understands its features and benefits. Providing ongoing training and support can help employees adapt to new processes and technologies more smoothly, minimizing resistance to change.
Engaging employees in continuous learning opportunities also encourages innovation and enhances the overall effectiveness of the MRP system.
Monitor and Adjust
Once the MRP system is in place, it is important to monitor its performance and make adjustments as needed. Regularly reviewing the system’s effectiveness will ensure that it continues to meet the evolving needs of the business. Feedback loops and performance metrics should be established to evaluate the system’s impact on productivity and cost-efficiency. By remaining flexible and open to change, manufacturers can optimize their MRP system over time, ensuring it remains a valuable asset in their operational strategy.
Conclusion
Material Requirements Planning (MRP) is a vital component of modern manufacturing operations.
By using MRP systems, manufacturers can streamline their processes, reduce costs, and improve product quality.
Understanding the key concepts of MRP and implementing the right system, like DELMIAWorks, can lead to significant improvements in operational efficiency and customer satisfaction.
As the manufacturing industry changes, using MRP systems will be important for staying competitive and achieving success. Investing in MRP technology helps manufacturers succeed now and prepares them for future market changes.
Contact us to learn more about DELMIAWorks’ in-built MRP System.