Real-time production monitoring in manufacturing is revolutionising the way industries operate.
It involves the continuous tracking of various processes and parameters within a manufacturing environment, utilizing advanced technologies and systems to provide immediate feedback.
This helps to optimise production and is important for improving product quality and operational efficiency.
In this article, we will look at real-time production monitoring. We will look at its benefits. We will also see how it works with manufacturing systems. This includes ERP software that helps support smart manufacturing.
Understanding Real-Time Process Monitoring
The Basics of Real-Time Monitoring
Real-time process monitoring refers to the use of technology to track and analyse the performance of different manufacturing processes as they occur.
This involves collecting data from various sensors, machines, and devices on the shop floor, which is then processed and displayed through dashboards for immediate analysis and decision-making.
The Role of MES in Real-Time Monitoring
Manufacturing Execution Systems (MES Systems) are pivotal in real-time monitoring.
They act as a bridge between the production floor and the enterprise systems, ensuring that data flows seamlessly across all departments.
By choosing an MES System embedded in your ERP (just like DELMIAWorks), manufacturers can gain shop floor insight and control over their processes, leading to a more paperless production floor environment.
This system provides a real-time production monitoring system that helps in identifying bottlenecks, reducing downtime, and enhancing productivity.
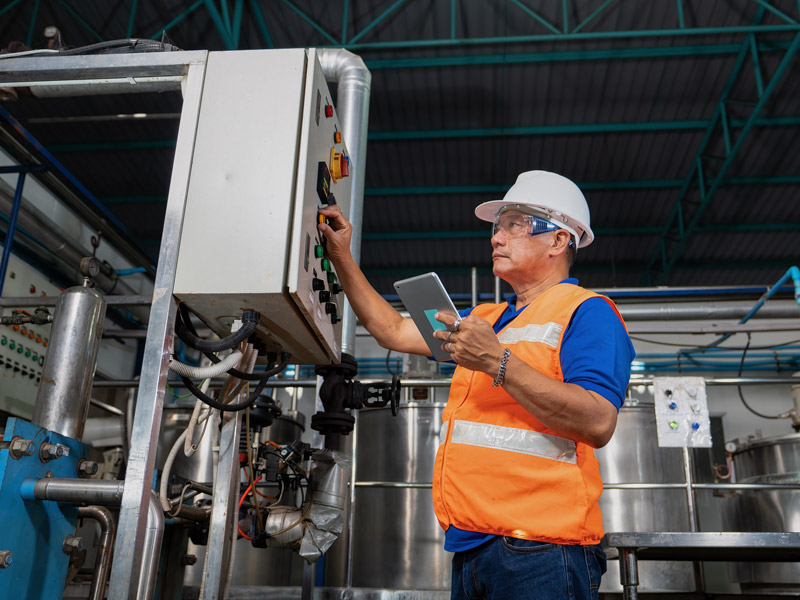
Advantages of Real-Time Monitoring in Manufacturing
Enhanced Production Efficiency
One of the primary advantages of real-time monitoring is the significant boost in production efficiency. By having a constant eye on the manufacturing processes, managers can quickly identify and rectify any issues that arise, minimising downtime and maximising output.
Improved Product Quality
Real-time monitoring allows for continuous quality checks throughout the production cycle. This ensures that any defects or deviations from the set standards are detected early, reducing waste and rework, and ensuring the delivery of high-quality products to the market.
Data-Driven Decision Making
With real-time data at their fingertips, manufacturing managers and business analysts can make informed decisions quickly. This data-driven approach enables them to respond to market demands promptly, adjust production schedules efficiently, and allocate resources optimally.
Transitioning to a Paperless Shop Floor
The Shift Towards Digitalisation
The move towards a paperless shop floor is a natural progression in the journey towards smart manufacturing. By digitising records and processes, manufacturers can eliminate the inefficiencies associated with paper-based systems, such as data entry errors, misplaced documents, and slow information retrieval.
Benefits of a Paperless Production Floor
A paperless production floor offers several benefits, including reduced operational costs, enhanced data accuracy, and improved environmental sustainability.
Moreover, it facilitates real-time process monitoring by ensuring that all data is recorded and accessible digitally, providing a complete view of the manufacturing environment at any given time.
Choosing the Right MES System for Your Needs
Factors to Consider
When selecting an MES for real-time monitoring, it is essential to consider factors such as the system’s integration capabilities, user-friendliness, scalability, and support services.
An effective MES should seamlessly integrate with existing ERP systems and provide comprehensive shop floor insight.
Implementing an MES System
Implementing an MES System requires careful planning and execution. It involves understanding the specific needs of your manufacturing processes, training your team on the new system, and continuously monitoring its performance to ensure it delivers the desired results.
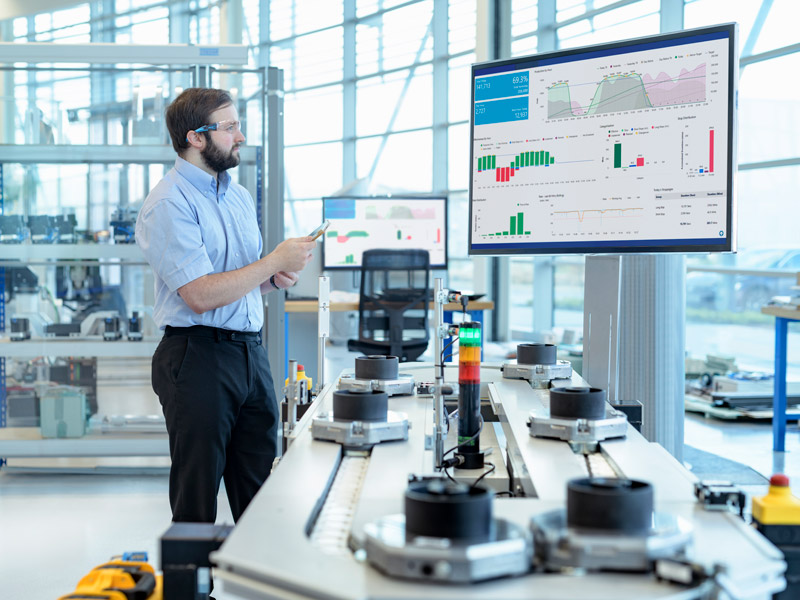
The Role of Industry 4.0 in Real-Time Production Monitoring
Embracing Smart Manufacturing
Industry 4.0, characterised by the integration of cyber-physical systems, the Internet of Things (IoT), and cloud computing, is driving the evolution of real-time monitoring production in manufacturing.
These technologies enable manufacturers to create a connected ecosystem where data flows freely across all levels of the organisation, facilitating smarter and more efficient operations.
Real-Time Process Control
Real-time process control is a critical component of Industry 4.0. By leveraging IoT devices and advanced analytics, manufacturers can achieve unparalleled control over their processes, ensuring optimal performance and quality at all times.
Conclusion
Real-time monitoring in manufacturing is a game-changer for industries looking to enhance efficiency, improve product quality, and stay competitive in a rapidly evolving market.
By integrating advanced systems like MES System and embracing the principles of Industry 4.0, manufacturers can achieve a level of operational excellence that was previously unattainable.
As you consider implementing real-time monitoring in your manufacturing processes, remember that the key to success lies in choosing the right technologies and systems that align with your specific needs and goals.
With the right strategy and tools in place, the journey towards a smarter, more efficient manufacturing operation is well within reach.
Contact us to find out how real-time production monitoring can help your manufacturing operation be more efficient.