Earlier this month, our colleagues from Dassault Systemes and DELMIAWorks ERP presented a webinar entitled: Smarter Automation – Bridging Your Process Equipment and Enterprise Management Solution.
Here is a transcript of that webinar. You can also access a copy of the presentation slides here.
Smarter Automation webinar transcript
My name is Arjun Bingipur. I work as an Industry Process Consultant for DELMIAWorks, based in Cambridge, in the UK.
In this webinar, we’ll be seeing how to achieve smarter automation by bringing together your process equipment and enterprise management capability. So, let’s talk a little bit about why we are here today.
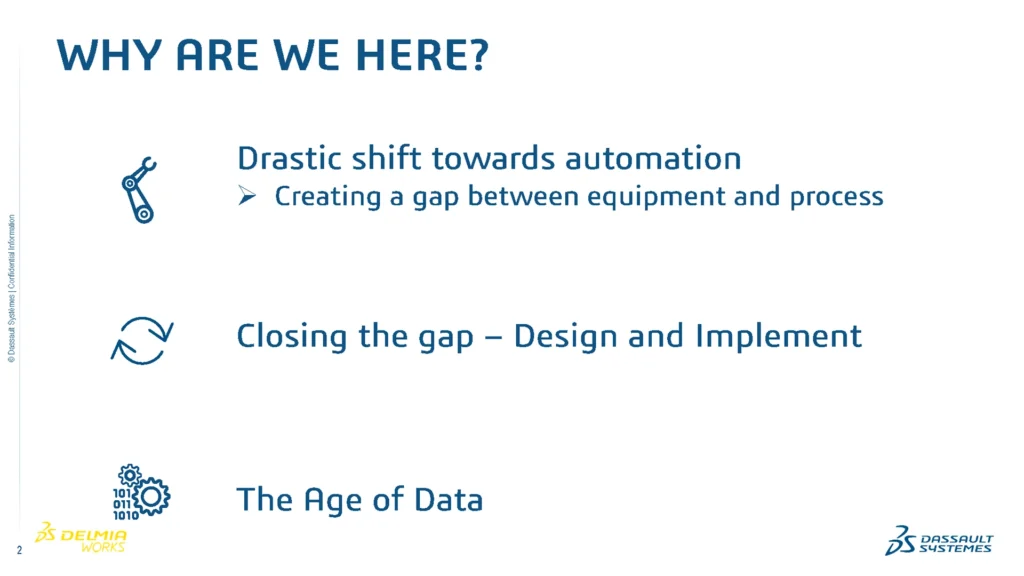
Firstly, I’d like to take some time to talk about the automation market in general. We have seen massive growth in automation technologies and the utilisation of automation tools up and down the manufacturing spectrum, from multi-million dollar corporations all the way down to small operations.
Then, we’ll look into some of the gaps that exist in terms of the design and implementation of these automation tools and some strategies we have used to bridge or close those gaps.
And finally, I want to talk about what automation means in terms of manufacturing operations management.
Automation equipment market growth
Automation is great. It’s fantastic. And we are seeing an increase in the use of robotics and other automation capabilities, which is definitely a step in the right direction.
But what does that mean for your downstream processes?
Let’s now take a quick look into the automation equipment marketplace. One of the things that we have seen that is pretty consistent is that the cost of automation equipment is continuously dropping, which allows us to gain easy access.
At the same time, as technology improves, the risks are decreasing. It’s easier to purchase, and the size of the organisations that could benefit from this technology is certainly going down.
Here is a McKinsey study that demonstrates what we are talking about. According to the study, there has been a 58% reduction in the prices of manufacturing automation equipment since 1990, as shown by the red downward slope in the graph that you can see.
At the same time, we all know that the cost of labour has been increasing, which is the blue upward slope.
Now, the one thing that is important to note here is that the data is relatively old; it’s from 2017. So, you can only imagine how the trend would be currently.
Integrating shop floor machines
And the flip side of the coin is machine integration. OEMs and manufacturers are setting up their products to integrate with other systems.
As an example here, there is a CNC centre from DMG Mori. It’s easy to configure as a machine just by visiting their website.
Now, the beautiful thing about this is that we do have the option to utilise their equipment, like their pick-and-place robots or their staging systems, or we can bring our own.
So, we are able to design our automation equipment to be able to integrate and interact with other multiple systems and machinery, and the entire market is positioned that way.
What does it mean in terms of integration and implementation?
How have these new technologies affected the way that we design our automation equipment and the way we manufacture?
I’d like to highlight a couple of significant gaps. The first one being the under-utilisation of equipment on the shop floor.
We are all pretty familiar with situations where we have an ideal piece of equipment that we would want to implement, and we haven’t gotten anywhere.
So, there’s a new pick-and-place robot that was purchased maybe a few months back, and it now has a quarter inch of dust on it because we really don’t understand how to utilise it.
Integration, data and control
We just don’t understand the fundamentals: how do we integrate it, how do we power it, how do we control it?
But also, we get into situations where people experience paralysis by analysis. We have these great tools, but we are not really sure how best to utilise them.
So, we get into these deep studies to figure it out, and it ends up slowing down the entire process.
The other thing that we are seeing is the creation of siloed systems.
Let’s say if you have a robotic system that’s either counting the parts or is performing some quality check, and it’s doing a fantastic job, but because the machine is not integrated with an upstream or downstream process. We end up in a situation where somebody has to go in manually and record that information.
The system just counted parts that are going into boxes, and it just did that for pallets, for example, and now we have got to take that information and put it into another system manually.
And that siloed infrastructure is really just creating more work for people. Those are the things that we want to try and avoid.
This is now a good segue into a real-world example in which you can see how we addressed such challenges in automation.
We (DELMIAWorks) recently collaborated with an industrial technology company called Airskin, based in Vienna, Austria.
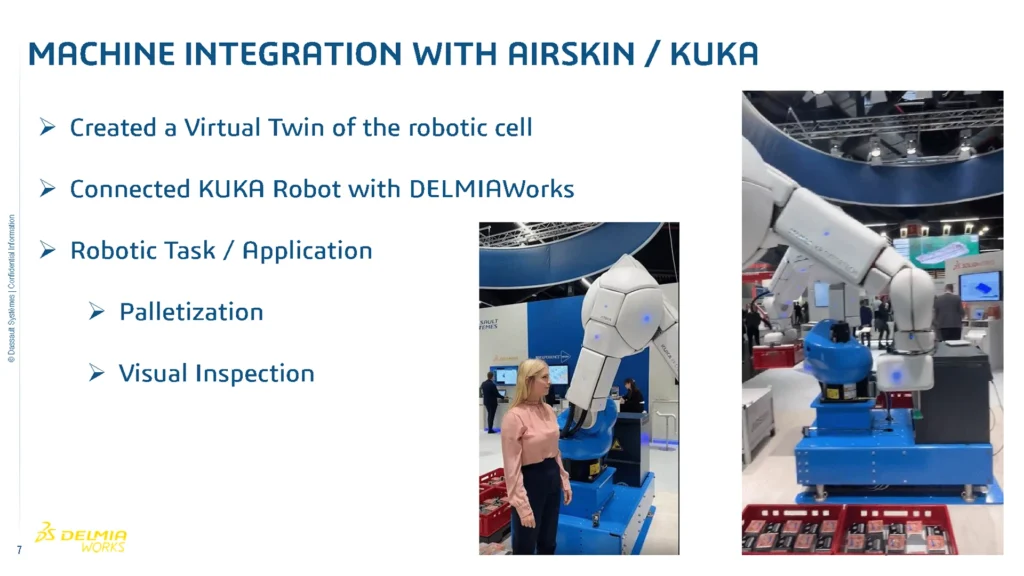
The company has developed a patented pressure-sensitive skin that can be mounted onto any standard industrial robots, or even AGVs, or any moving machinery, focused especially on palletising, vision inspection, screw driving applications, and so on.
The image on the left is a typical robot cell with a safety fence around it, and on the right, you can see the same manufacturing cell which has a touch-sensitive skin mounted on the robot.
The company’s main focus is on safe human-robot collaboration by upgrading standard industrial robots to fenceless collaborative applications.
Fenceless applications from Airskin aim to solve some of the challenges manufacturers typically face, such as the high cost for fence construction, longer return on such investments, and primarily limited real estate on the shop floor.
Here you can see three KUKA robots in action. One robot is moving boxes from location A to location B, and each box typically contains 15 chocolate wafers.

The small robot in the middle is performing an in-process visual inspection by counting the number of wafers in the box. And if it is less than 15, it will pick up additional wafers as needed with its suction head and then count the boxes so that the count is always 15.
Finally, the big robot is performing a final inspection. It is scanning every box that is being placed and counting the number of wafers in each box. Before we began integrating with these robots, the first step was to create a virtual twin of the robot, and then the next step was to connect to the robots in real-time to receive continuous feedback on what’s happening on the shop floor.
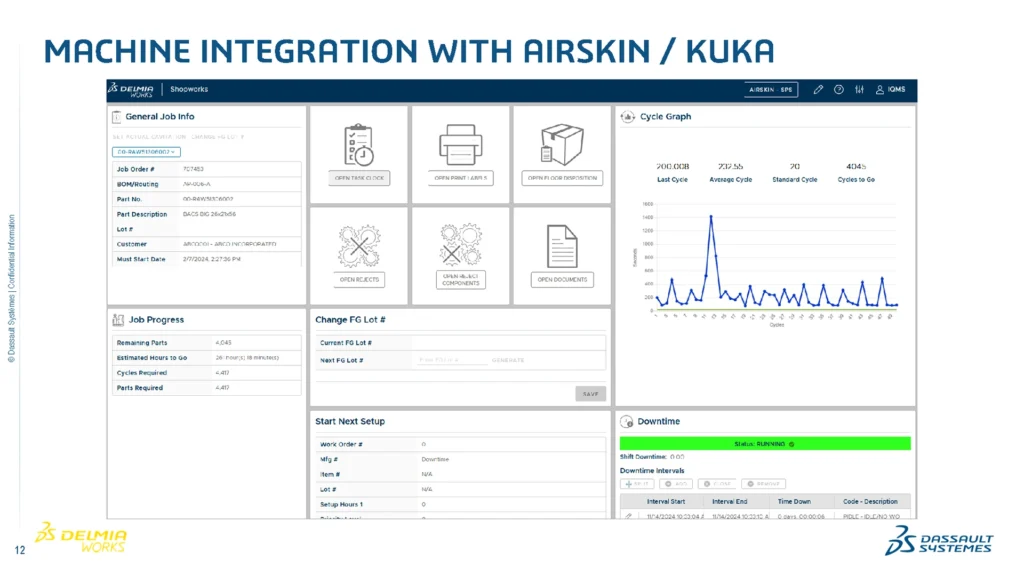
Using DELMIAWorks’ robotic programming capability, Dassault first created a virtual robotic cell using the available 3D data for these robots.
So, we mimicked the process, what was going to be happening, even before we placed the machines on the shop floor.
We then configured and simulated the movement of the robotic arms for safety and collision, as to what degree the arm can move and stretch without coming into contact with each other.
We also simulated the box movements and visual inspection changes. And this is where we start to bridge the gap between what the equipment is doing on the shop floor and what process we are planning to fulfill.
PLCs and the role of MES Systems for real-time monitoring
Once the connectivity was established with the PLCs on the robots using the DELMIAWorks manufacturing execution system, it was time to bring it all together with the data being received in real-time.
Using real-time charts within DELMIAWorks, we were able to set up dashboards quickly to monitor three key data points.
Chart one, as you can see, is displaying how many boxes were moved from location A to location B. So, this is just a series counter that increments by one every time a box is moved. Chart two is displaying in which position the box was placed.
So, there were four positions defined initially in the previous step, and this chart simply displays either position one, two, three, or four. And finally, chart three displays the result of the visual inspection, and in this case, we have defined a target value of 15, which is the count of wafers we expect to see in each box.
So, moving further, we also set up statistical process control at the final visual inspection stage, and using the SPC trend charts, we could easily see whenever there was a quality event.
And in this case, whenever the wafer count dropped below 15. And you can see on the bottom of the screen, alarms are being triggered. So, how was this machine integration achieved?
The robots, in this case, had a Siemens Simatic PLC.
We connected directly to the controller using OPC UA, which is one of the most common industrial protocols for machine connectivity.
Once we established the connection, we could browse the PLC for tags that were relevant to us. As you can see on the bottom left-hand section of the image, there are a bunch of tags or variables available on the PLC, but we were only interested in three tags that are highlighted in the middle section for our use case.
MES Systems + ERP bridges the automation & process gap
Finally, what does it mean for the rest of the downstream process in terms of how many parts have been manufactured or are we ready to ship this out?
What was the total cost associated with the manufacturing process?
Was there any downtime during production? What did the average cycle look like, and so on?
Because this is all tied back to the manufacturing execution system and also the ERP solution, we have access to all of that information, and we can easily answer these questions either with a click of a button or by configuring specific dashboards.
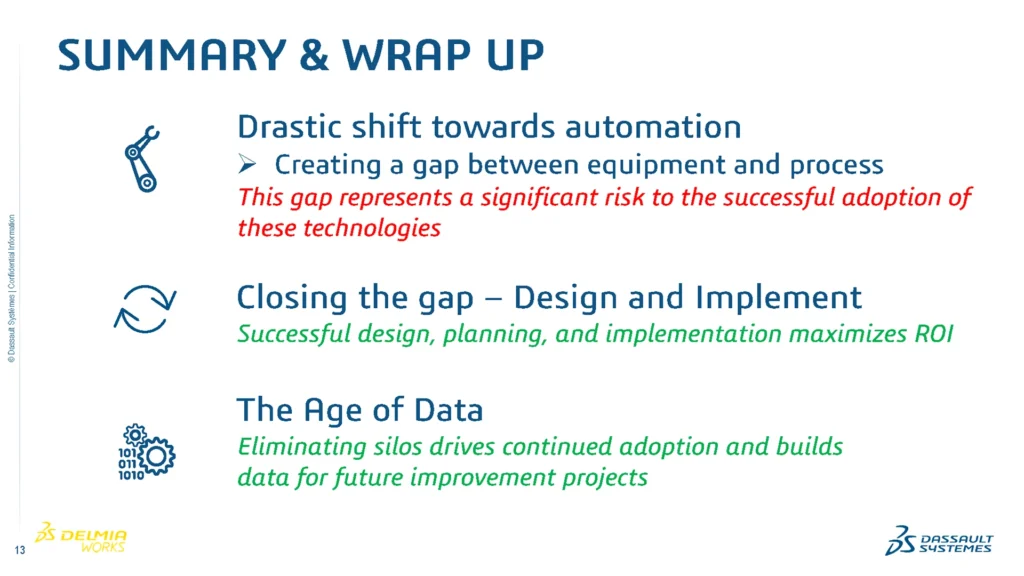
To summarise and wrap up, any automation journey has the potential to create a gap between the equipment and the process, and these gaps represent a pretty significant risk in achieving the financial goals with those capital investments.
We talked about how trial and error on the shop floor could also lead to wasted time, opportunity, and cost early on.
Space is often limited in manufacturing facilities, and if we are occupying this space for weeks or months, in some cases, trying to figure out the optimal use of these technologies, we are losing productivity, money, and capacity.
We are also losing our ability to meet customer demands. We also talked about how the design and planning stage of this adoption process really allows you to maximise that return on investment without significant burden on the shop floor.
Going back to the example of our integration with the Airskin and KUKA robots, the whole exercise was delivered on two key elements.
First is that even before we started placing the robots on the shop floor, we created a digital twin. We didn’t waste time figuring out on the shop floor in what fashion the robots needed to be placed or how they were going to be used. This was all designed and simulated in advance. And then finally, we talked about how these equipment can be easily integrated into the manufacturing execution software so that we can eliminate data silos.
So, production reporting doesn’t have to be manual. Quality data doesn’t have to be tracked manually, especially in this example, where vision systems were being used, and it’s becoming very popular and less expensive.
Q&As
So, with this, we can open up for Q&A. Feel free to type in any questions you might have in the chat box. So, there are already a couple of questions that are coming in.
Communication protocols
So, one of the questions is, are there specific communication protocols that we should be looking for in equipment?
As I said before, the most famous or most common industrial protocol currently is OPC UA. But having said that, there are multiple protocols that we support. For example, MQTT, and there is MTConnect. And also, we also support a wide range of protocols like EuroMap, Allen-Bradley, and so on.
There are a lot of options, a lot of choices that we can look into. And there’s one more question coming in in terms of sticking with the PLC communication. Are there any other options if PLC communication isn’t an option? Well, this is a good question because we see a lot of different variations of machines on the manufacturing floor.
Some are quite new, networked, and have a PLC on them. At the same time, there are other legacy machines that are not networked.
So, when we have a legacy machine, one option is, of course, to add a PLC onto that machine, and sometimes it is not possible or cost-prohibitive, in which case we have our own hardware which can be connected to these older machines.
And once we plug in this piece of kit to the legacy machines, we will then be able to grab the data just like we do from a PLC. So, we pretty much achieve the same connectivity that we have from a PLC. So, that would be the most relevant option for legacy machines.
DELMIAWorks ERP software
Okay, so one more question I can see is, can you tell us a little bit more about DELMIAWorks? Sure, yeah.
So, DELMIAWorks is an integrated ERP and MES solution. It’s got a native shop floor capability, especially for shop floor operators, where they can log into a touch screen device or a tablet and then see what’s happening with the machines on the shop floor.
And DELMIAWorks has a full-fledged maintenance, repair, and overhaul, and quality suite integrated as part of the solution.
And it has got native integrations built into SOLIDWORKS and also to the 3DEXPERIENCE platform.
Contact one of your resellers or come back to us for more information on DELMIAWorks.
Interested in learning more about Smarter Automation?
These articles should be of interest: